DEVIATION MANAGEMENT SOFTWARE
Software for your digital deviation management
Optimize your deviation management with seamless digital workflows and automated process control to ensure the quality of your products and services.
Real-time overview of all deviation processes
Automated forwarding and escalation management
Consideration of internal and legal requirements
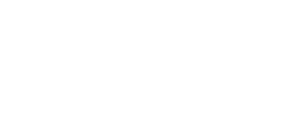
You are currently viewing a placeholder content from YouTube. To access the actual content, click the button below. Please note that doing so will share data with third-party providers.
More Information» dls | deviation control «
Software for effective deviation management
Control your production-related quality management processes, in particular the reporting of deviations (deviation control), with our innovative digital workflows. Our comprehensive solutions completely transform your previous paper-based processes into a digital format, from recording to closing.
The workflow system ensures that the digital deviation form is automatically forwarded to the relevant department. If a deadline is missed, a reminder and escalation management system ensures that no deadlines are missed. The system also includes a rule for substitution in task routing to guarantee seamless processing and traceability.
How can you benefit from the Deviation Control software solution?
Data integrity
Deviation reports are no longer lost as they are stored electronically from the outset.
Process safety
The workflow system ensures that each deviation is forwarded to the responsible specialist addressee after each step. An escalation system takes effect if deadlines are not met.
Increased data security
Protect your sensitive data from unauthorized access and potential threats from harmful influences. Our security precautions guarantee a high level of protection for your information.
Individual configuration
Let the modules be configured according to your wishes and preferences to facilitate the onboarding training for your colleagues.
Constant availability
Access your data at any time. It does not matter where you are.
Traceability
Deviation reports can be linked to other modules such as Corrective and Preventive Actions (CAPA) and Change Management (CC). Thus a traceable chain of interrelated individual processes is created.
More efficient process runtimes
Significantly reduce your process throughput times with the digital solution for deviation management.
Transparency
Every authorized employee has insight into the current status of all deviation reports, even if they are not directly involved in the process.
Central information platform
Use d.velop documents (formerly d.3ecm) as your central platform for quick access to all relevant data.
Reports
Create detailed reports and statistics on your deviations, e.g. to support your (PQR).
We would like to present you some features already
The digital forms are also converted to a PDF/A in parallel. This way, employees who are not involved in the process can also gain insight into the workflow and the document can be shared with external parties if required.
What is a Deviation Control process?
The purpose of the Deviation Control process is to ensure that products, processes, attachments and documents that do not comply with the defined quality specifications are identified, evaluated and subjected to a decision on how to proceed, and that the measures taken are implemented. Affected are products and processes, machines and systems that show a deviation or malfunction as well as deviations from regulations, established procedures and specifications that may have an impact on product quality.
The scope of application concerns
- Production
- Quality control
- Quality assurance
- QM Officer
- Qualified person (QP)
- Galenics
Every action in the process is automatically documented by the system accordingly. Integrated audit trail functions ensure high traceability.
The digital form is filled out step by step and provided with the relevant entries and data. Fields with a blue background are mandatory. Predefined value sets and drop-down functions make it easy for users to fill out the form.
After processing the individual steps (1. Initiation, 2. Cause determination, 3. Risk consideration, etc.), the workflow system automatically sends tasks and messages to the responsible agents or workflow participants. Once all steps have been processed, the workflow is considered complete.
1. Step: Initiation
The recording of a deviation can be done by any employee. After the relevant data has been entered by an employee, the person who will process the causes is determined automatically or can be selected manually, depending on the configuration. For example, the process can be sent to the head of the organizational unit (e.g. department head). If, for example, the employee is the head of the organizational unit, he or she is automatically the recipient of the cause determination process step.
Would you like a live insight into the software?
Gain a comprehensive live insight into the possibilities of production-related quality management processes within just 45 minutes using a specific use case. Learn how you can use Digital Life Sciences solutions to optimize your production-related QM processes, such as complaints (Complaint Management), deviation reports (Deviation control), corrective and preventive actions (CAPA) and Change control efficiently through our digital workflows.
Some features of Deviation Management
- Automatic PDF creation and storage of the form in the eDMS after each step
- Automatic classification of the deviation based on the metadata entered in the form
- Referencing master data from your ERP system
- Adding documents, such as digital photos, to your DC form
- Initiation of the individual tasks for the further processing of the workflow
- Escalation messages both within the system and by e‑mail
- Integrated absence management
Our Deviation Control process complies with the following regulations
33 Good reasons for a cooperation with Digital LS
You’re not convinced yet? You’re not convinced yet? Find out about 33 good reasons speaking for a cooperation with Digital Life Sciences GmbH. We will show you reasons from the provider’s point of view, from the software point of view and other general reasons that distinguish us.
Customer review on the Deviation Management
"We have been a customer from the very beginning and Digital Life Sciences supports us reliably and sustainably with their products and thus helps us to further develop our QMS and to implement electronic solutions / workflows regarding the requirements for data integrity."
You might also like…
Deviation management is a component of the Digital Life Sciences solution suite. Each product is powerful on its own, but when used together they are even better.
Document Control software
Whether work / process instructions (SOPs), process descriptions, test specifications or other types of documents — you can create, revise and sign them all digitally with the document control software.
Training Management software
Extend the “Document Control” module to actively plan and record the qualifications of your employees with our training management software.
E‑learning software
Use the new software “E‑Learning” to train your employees digitally. Create an e‑learning course according to your wishes using Microsoft PowerPoint or integrate existing presentations.
Frequently asked questions (FAQs) about Deviation Control
Are the contents of all process steps visible?
When working on a process step, only this step can be processed, but the other process steps are still visible.
Can the predefined designations be changed?
In the workflow administration, you can configure the names of the process steps, field names and datasets.
Can the predefined steps be customized?
The Deviation Control process flow has been designed in accordance with the GxP regulations and created in consultation with QM experts. Against the background of the validation documentation, the process steps are therefore mandatory. However, each process step contains a ‘Custom Panel’, which can be used to display further information or initiate actions.
Can tasks be delegated?
In all process steps that follow the initiation, you can forward the process step to another person. The recipient’s authorization is checked during the selection.
Can I analyze the Deviation Controls?
The essential data of a Deviation Control is transferred to the attributes of the data record. This allows you to search and analyze the Deviation Controls you have created. The analyses can be exported as PDF, EXCEL or WORD documents.
Are there time limits for the execution of the process steps?
In the administration, time specifications can be entered for each process step. Reminder messages are sent before the process steps are due. The reminder message is sent to the processor of the task, the coordinator and the configured group that is to be informed about the reminder (for example, QA). A reminder is sent with the configured subject.
Can a process be cancelled?
It can be configured so that the process can be cancelled at any process step. For the cancellation, it is required to indicate a reason in a mandatory field. Only the coordinator of the process is allowed to cancel.
Are there templates for measures in a Deviation Control?
Having entered a measure, you can save it as a template in the measure table. The templates are available for insertion in a Deviation Control. The due date for the measure is calculated based on the duration entered in the template.
Can process steps be subsequently corrected?
In principle, a process step is completed with an electronic signature and can no longer be corrected. With the function ‘Step back’ the process can be returned to a previous process step. The user who has completed this step receives it again for editing and the process continues from this step. Any return to a previous step is recorded in the audit trail.
Can attachments be stored with a Deviation Control?
If additional files are required for a process, attachments can be uploaded in all process steps and linked to the current process. The attachments are stored under a corresponding document type in the DMS and can be viewed in the Deviation Control under ‘Attachments’ by all process participants. You can configure which file types can be saved as attachments and how large the files can be.
Quick contact
Do you have a question about the Deviation Control module?
Our sales team will help you promptly and gladly.