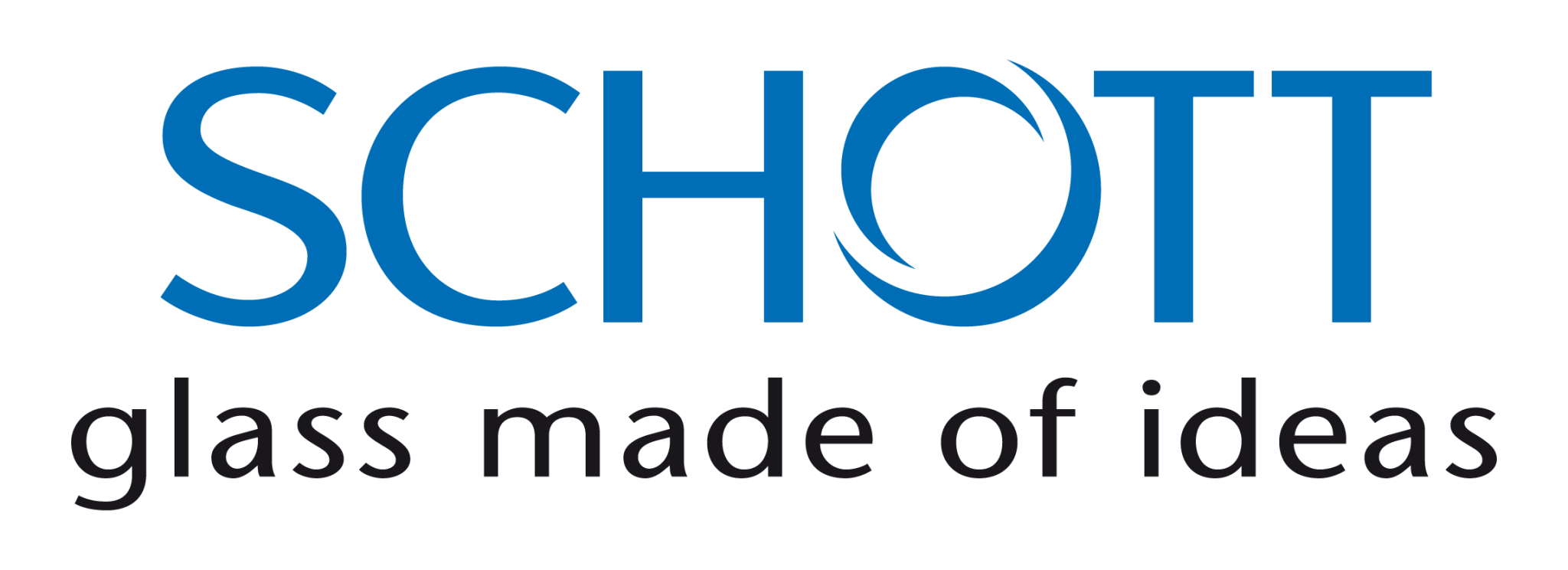
SCHOTT AG optimizes QM processes for document control and improves workflows worldwide with innovative electronic quality management system d.3 eQMS
"Historically, six of our business units had their own document management system, purchased separately and established their own structure. With the introduction of a new electronic quality management system (eQMS), we wanted to optimize, centralize and harmonize cooperation in the quality management units. This way, the units can help each other much better. We were able to create areas, with documents such as standards, sets of rules or guidelines, which all units need, but which only have to be maintained once. This allowed us to become more efficient and also save money. I would also like to emphasize the validation of computer-aided systems, where Digital Life Sciences has helped us significantly"
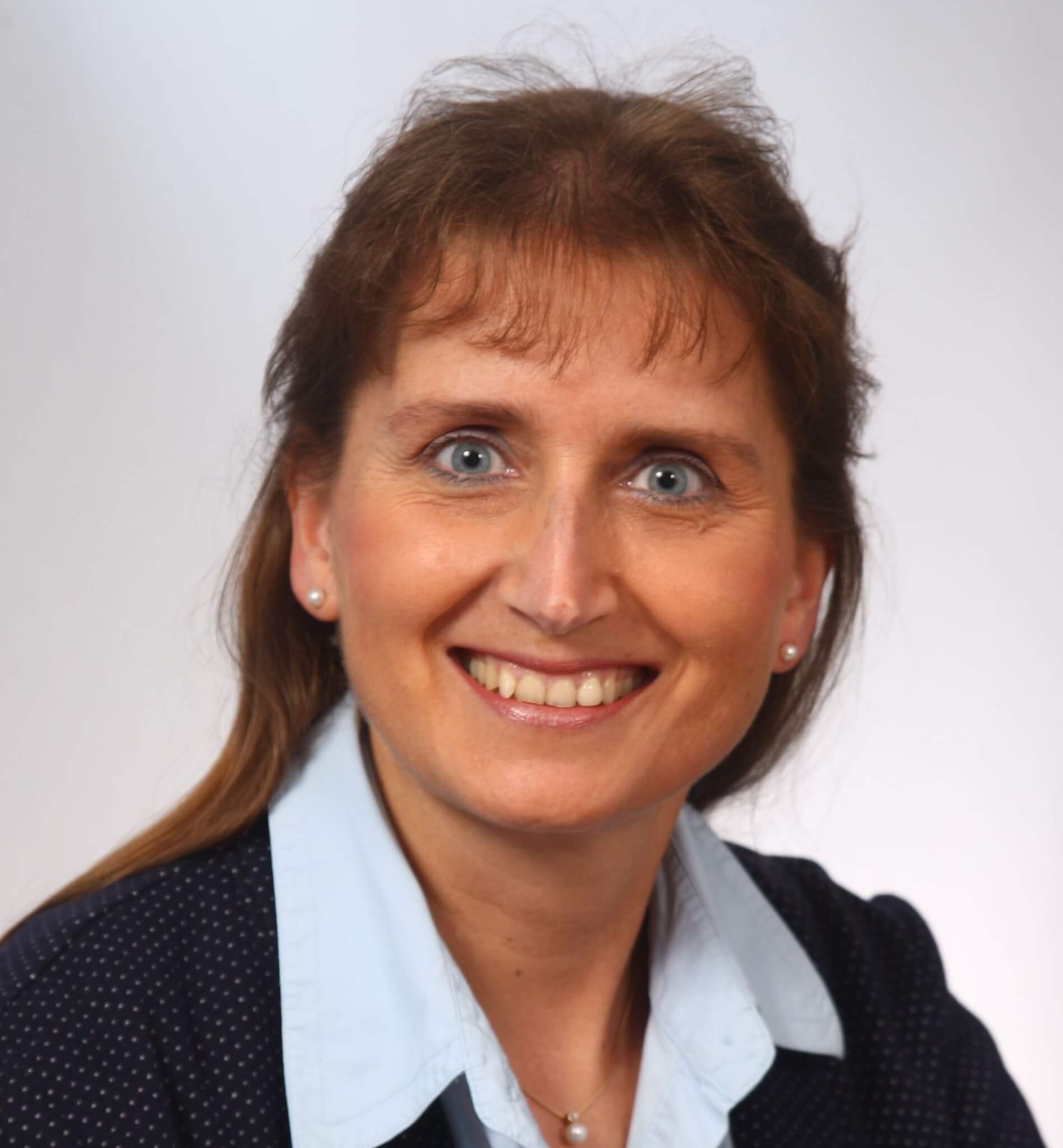
What do pharmaceutical vials for the COVID-19 vaccine, ceramic cooktops and mirrors for the world’s largest optical telescope have in common? The high-tech products are manufactured by SCHOTT AG, an international technology group with over 130 years of history.
It all started at Otto Schott’s parents’ house in Witten, where the chemist invented a new type of glass in 1879 – lithium glass. It had completely new optical properties. The then 28-year-old sent a sample of it to the renowned physicist Ernst Abbe in Jena. A fruitful collaboration begins, Schott settles in Jena. There he invents a heat-resistant glass that does not shatter when boiling water is poured into it: Jena glass. One of the cornerstones of today’s SCHOTT AG with subsidiaries in 34 countries.
Today, the AG is a sought-after partner for industrial sectors worldwide in which goods at the cutting edge of technological development are required: Medicine, pharmaceuticals, electronics, optical applications, power generation, automotive, aviation and, last but not least, astronomy. In 2021, the approximately 16,500 employees generated sales of over 2.5 billion euros.
SCHOTT AG has become indispensable in the pharmaceutical industry, among others. With over 600 production lines in 13 countries, the company manufactures over 11 billion syringes, vials, ampoules and specialty items. SCHOTT relies on selected raw materials and the most reliable and latest production processes. As a result, the company could ship more than one billion vials of COVID-19 vaccine by early March 2021.
In this context, SCHOTT not only relied on state-of-the-art manufacturing methods, but also on up-to-date software to manage documents and comply with documentation obligations and other requirements for processes in the pharmaceutical industry. So far, so good.
Central management of the d.3 eQMS, but room for maneuver for each business unit due to structuring by client
But the devil hid in the details. Several business units and corporate functions at various locations worldwide used the existing document management system: Advanced Optics, Hometech, Lighting and Imaging, Research and Development (R&D), as well as the Accredited Test Laboratories of SCHOTT AG. The only catch: Each unit purchased the software itself, established its own structure and used the existing software in its own way. Regulations had to be found that enabled the clients to support their respective processes in the production environment or corporate functions with document control and to fulfill the quality-relevant requirements worldwide. “Ultimately, all units struggled with the same document control challenges. We wanted to centralize and harmonize that”, says Christine Strubel, head of “Management Systems Quality & EHS”.
Thus, the international orientation and availability of several languages was also an important criterion in the selection of a new document and quality management system.
In the age of digitalization, the task was to establish a promising product in cooperation with the central IT of SCHOTT AG that supports the SCHOTT IT policy, but also fully meets the requirements of the business units and corporate functions at the same time. The product d.3 eQMS from Digital Life Sciences GmbH can fulfill the requirements.
Qualify employees digitally - without manually maintained Excel lists
Another weakness of the existing document management: Digital training management was missing. “We didn’t have that in the old system”, describes Strubel, “if there were new trainings or guidelines, the relevant employee would just get an email with a reference to the new guidelines. In parallel, we maintained Excel lists and paper folders to keep track of which colleague had participated in which qualification measure.”
Consolidation of six independent systems
Now good advice was expensive. Christine Strubel started looking for alternatives. In January 2018, she got in closer contact with Digital Life Sciences GmbH, which specializes in GxP-compliant documentation solutions.
The solution: the electronic document and quality management system (d.3 eQMS) of Digital Life Sciences GmbH. This offers the business units the possibility to store and manage documents beyond silo boundaries. But that’s not all.
Document control and digital workflows with dls | eQMS
Once installed and set up, the dls | eQMS enables essential functions for a company. The following requirements were vital for SCHOTT AG:
- Fast search and access to digital information, depending on roles and workflows, independent of departments and business units
- Acceptance by the users of the system due to excellent usability
- Worldwide use and provision of a system interface in multiple languages
- Training Management
- Easily meet increasing documentation and quality management requirements
- Fully validated system according to compliance requirements such as GAMP 5, EU Directive, etc.
- Expansion and extension of the functionalities through the use of further modules, such as:
- Change Management
- CAPA Management – Corrective And Preventive Action, a practice in quality management and part of GMP-compliant work (“Good Manufacturing Practice”)
- Deviation Control
“We were also interested in saving costs and time and increasing efficiency”, describes Christine Strubel: “We also wanted to save money through the targeted management of documents and regulations. We manufacture products for the medical and pharmaceutical sectors, where there are high requirements for documentation, and the system should support this. But the good price-performance ratio was also a deciding factor. In addition, a standard product should be introduced that already meets compliance requirements to the extent that no special programming is required, only customizing.”
First business units started in 2018 with the introduction of the new d.3 eQMS
In September 2018, two business units were launched with dls | eQMS. SCHOTT worked closely with Digital Life Sciences to merge the various documents. The task was to avoid duplicates, model suitable digital workflows, and design appropriate user and authorization groups. More than 50,000 documents from six differently parameterized, outdated document management systems were merged in this way.
The work progressed so quickly that the first two units, the Accredited Test Laboratories of SCHOTT AG and the Lighting and Imaging Business Unit, were able to go live in January 2020, less than a year and a half after the project started. Strubel: “The experience we have gained has been extremely good. I would also like to highlight the validation of computer-aided systems, where Digital Life Sciences has helped us significantly.”
When merging and migrating existing data into a modern document management system, not only must all parties involved be able to rely on each other. It also pays to proceed with tact.
Dr. Dennis Sandkühler is well aware of this: “We have always oriented ourselves to our own standards when it comes to setups. We didn’t want to bend ourselves or the business units, and we certainly didn’t want to change the whole organization.”
Validation of computer-based systems: "par excellence consulting"
SCHOTT benefits from the experience of Digital Life Sciences in the pharmaceutical and medical sectors: “Many of our standards and regulations, such as ISO standards or regulations for medical devices, have been reissued in the past year and a half,” says Christine Strubel, “and these rules often include the requirement that computerized systems must be validated. This is very extensive, and Digital Life Sciences advised us par excellence.”
Time-saving workflows through digital document management
It therefore did not take long for the other business units to follow suit after the pilot phase. Over 3000 employees at SCHOTT locations from North America to Malaysia benefit from dls | eQMS. Christine Strubel: “We have so many new opportunities with the dls | eQMS that simply didn’t exist before.”
For instance:
- Digital workflows with profiles and roles: Verification and approval within processes. An example from document creation: If an approval process stops because one of the employees who could approve goes on vacation, the process continues with another colleague who is also allowed to approve – such as the head of department.
- Deviation management and CAPA: dls | eQMS supports the logging and correction of deviations and currently supports the accredited testing laboratories of SCHOTT AG to fulfill the requirements of DIN EN ISO/IEC 17025 and GMP requirements. Change processes, also within the d.3 eQMS, are documented and released with the help of Change Management.
- There is no need anymore to send Office documents back and forth by e-mail, for example, which is prone to errors. This alone increases quality and speeds up processes, because thanks to dls | eQMS, SCHOTT employees know that the documents are always up-to-date and do not have to search for the version for a long time – e.g. thanks to the full-text search function.
- Training Management (Training Management): SCHOTT can now train employees with any documents just in time, with vouchers, digital electronic exam and even tests. If a new training document is available, the relevant employees receive a message from dls | eQMS informing them that they must complete the training or read the updated rules and regulations. Once this is done, employees acknowledge the training. dls | eQMS provides quality assurance with an overview of which employee has which status and which training is in which phase.
“Training management in particular helps us enormously,” says Christine Strubel, “we didn’t have that before, we kept track of it manually in an Excel file. With the many training sheets, it was a huge effort, now we have a very nice overview in the dls | eQMS system. It’s also very well received by the staff.”
Strubel’s conclusion: “We have chosen the right product. Our high demands on usability have been met, the search function in dls | eQMS alone is excellent. That wasn’t bad in our previous system either, but it’s better now. After the training courses and getting used to the system, it’s now much easier to manage all the documents.” The combination of the different modules in the d.3 eQMS enables an extension and expansion of the system and also offers further options for the future.
Learn more about the training management
Get a comprehensive overview of our versatile training management solution now.