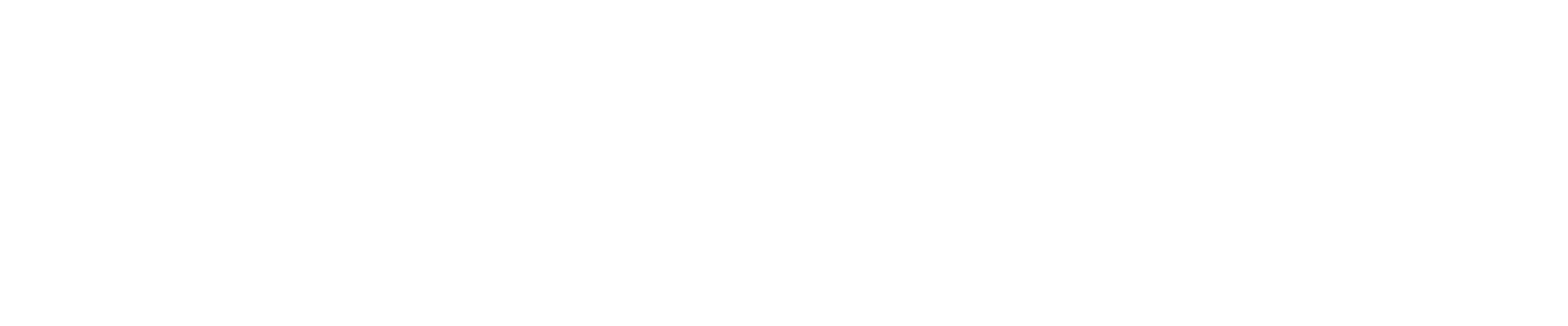
Without risks and side effects
"With the Digital Life Sciences team, we implemented our new GMP-compliant DMS and training tool in a very short time. Due to the competent consulting, a pragmatic solution for every problem was quickly found and also the dreaded data migration from our old system was successful thanks to the database specialists of d.velop. With the introduction of DMS and Training Management and the commitment of d.velop, we have taken a big step towards system optimization. The enterprise team of Hennig Arzneimittel says Thank you and we'd be pleased to do it again!"
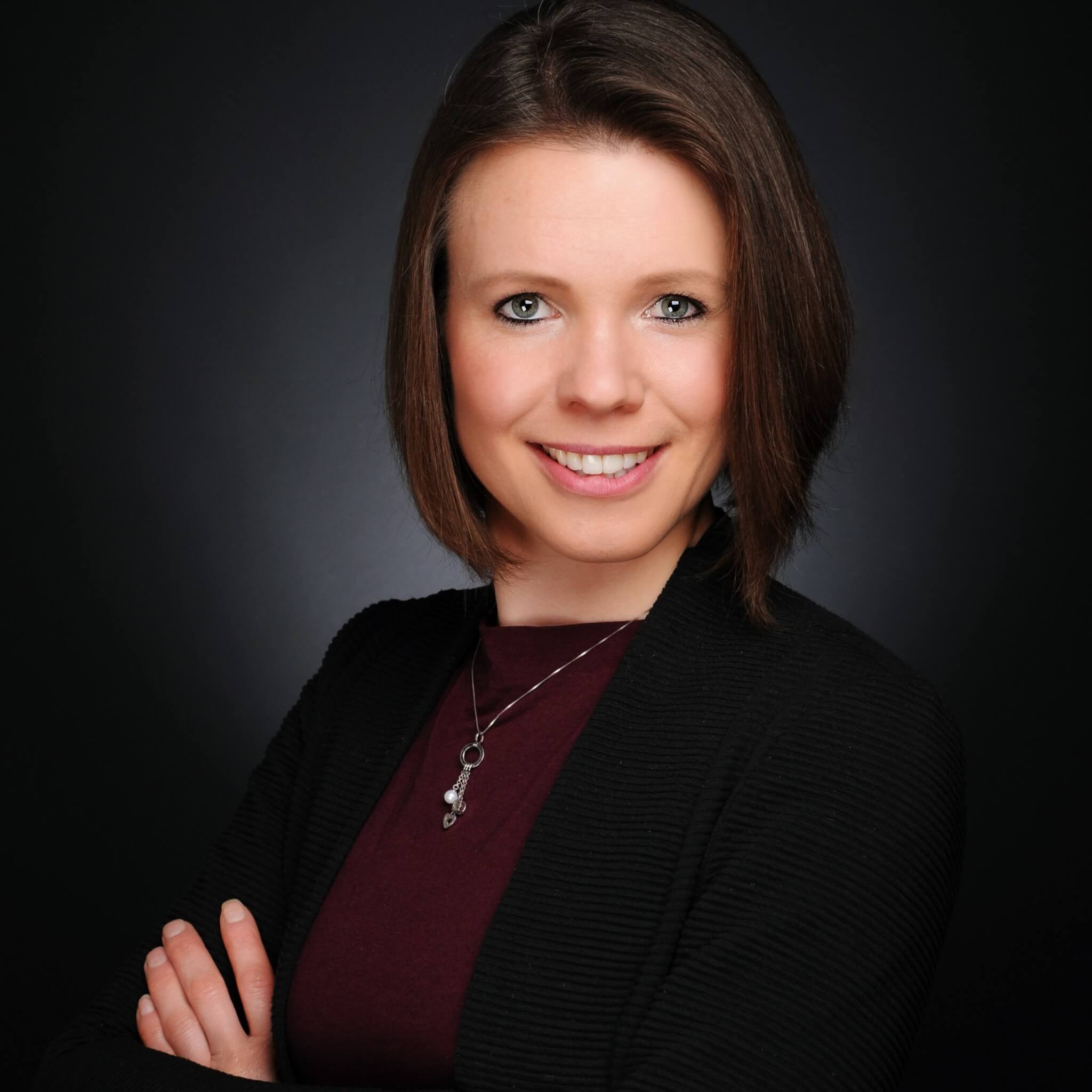
How the family business Hennig Arzneimittel benefits from a modern eDMS/eQMS
The medical and pharmaceutical industry is struggling with high legal requirements for the management of documents. The family-owned company Hennig Arzneimittel therefore relies on a document and quality management system (eDMS/eQMS) by Digital Life Sciences – and at the same time speeds up work processes.
The history of Hennig Arzneimittel goes back to the year 1898. Max E. Hennig, a 23-year-old chemist, founded the company in Berlin. In the beginning he exclusively produced tinctures from organ and plant extracts. Today, more than 120 years later, the company in Flörsheim am Main in Hesse has grown into a medium-sized enterprise with 330 employees and specialises in the production and marketing of numerous medicinal products, medical devices and food supplements, including a preparation for the treatment of vertigo and balance disorders.
Like all companies in the life sciences sector, Hennig Arzneimittel is also confronted with strict regulations. The pharmaceutical company must fully document all work instructions, test specifications and methods used in the manufacture of medicinal products. Since 2011, the company has performed this task with an electronic document management system (DMS). Employees thus have quick access to documents – the assistant at the incoming goods department, for example, has access to checklists for goods acceptance while the employee in production can see new hygiene regulations.
No updates, no support: Old DMS made everyday work more difficult
Paper and filing cabinets should have been a thing of the past thanks to the DMS. In theory. Since the manufacturer of the DMS disappeared from the market, there was no support and no more updates. A volatile situation: “By law, we are required to keep all risks under control. We therefore made backup copies of all documents, printed them and filed them – just in case the DMS suddenly stopped working,” recalls Meike Murawski, QA Manager Validation and Projects at Hennig Arzneimittel. Kind of a backwards roll in terms of digitization. Despite DMS the filing cabinets were full.
In order to increase security and prevent media disruptions, Hennig Arzneimittel wanted to replace the old DMS with a new solution as quickly as possible. “We researched DMS vendors in the pharmaceutical sector and contacted three manufacturers,” says Murawski. “We quickly realized that we sympathize most with the experts from d.velop and trust their experience the most.” Digital Life Sciences serves around 130 customers, the majority of whom are active in the validated GxP environment, mostly in medical technology or the pharmaceutical sector.
New DMS puts an end to annoying paper backups
Together with Digital Life Sciences, Hennig Arzneimittel set up a new document management system between October 2019 and March 2020. The DMS contains all work instructions, manufacturing and test specifications as well as qualification certificates of the employees. “We now finally have a modern DMS with a reliable contact person and no longer have to worry about default risks,” Murawski is pleased to say. “This also means the end of cumbersome paper backups, which have unnecessarily consumed resources and space in the past.”
The new DMS also speeds up the signature management. If employees receive an instruction, for example for a new garment in production, they must confirm with an electronic signature that they have acknowledged the SOP (Standard Operating Procedure). The administrative burden is high in the traditional paper-based way. The electronic signature saves time. Instead of signing manually, the employee confirms the acknowledgement of the document in the DMS with user name and password. The e-signature is legally equivalent to a manual signature here.
The DMS provides basis for regulatory compliance
Thanks to the new DMS, Hennig Arzneimittel also benefits from legally compliant archiving. “We have to face exceptionally high document management requirements in the life science industry. With our DMS we manage and archive all electronic documents in a legally compliant manner. It is therefore the basis for legally compliant work,” explains Murawski. Moreover documents can be found in seconds using keywords, metadata, full text and faceting. “The system is intuitive to understand. We can view search results in detail and save search templates – that’s especially handy if you perform regular evaluations.”
"d.velop is really an absolute professional in the field of migration"
As intuitive as the new functions of the DMS are – the change from the old to the new solution was not. d.velop was faced with the challenge of migrating thousands of electronic documents from a system that was no longer maintained – including their metadata. Mistakes were not allowed to happen. They could jeopardize the daily work routine. For example, if employees suddenly start working according to wrong manufacturing instructions or if proofs of qualification get mixed up. “Migrating the documents with their metadata and merging them correctly in the new DMS were some of the biggest challenges of this project,” explains Dr. Dennis Sandkühler, Project Manager at Digital Life Sciences.
The migration was difficult because there were no interfaces between the old and new DMS. This meant that there were obstacles in the way of automatic data transfer. “We therefore analyzed the specifics of the old and new systems and developed a small, customized migration tool,” says Sandkühler. “After migration testing, we were finally able to use the software to automatically transfer data from the old DMS to the new one.” The migration was completed within one day, confirms Murawski. “d.velop works really professionally in this area.”
Nice bonus: New tool optimizes management of training courses
In order to optimize the management of trainings, Hennig Arzneimittel has also implemented a new training tool from d.velop parallel to the DMS. The former solution collided with the operating system of the EDP and was no longer updateable. “The old system also offered only poor performance, especially with large numbers of participants, and crashed too often,” Murawski recalls. “These problems have now been solved by the new training tool. We now plan and document trainings for employees better than ever.”
The training management tool is directly linked to the DMS. A qualification matrix informs department managers about the current training status of employees at the push of a button. This transparency did not exist in the past because the IT department had to run the old tool on a separate terminal server – it was no longer compatible with the operating system currently used by the IT department. With this makeshift solution, however, only quality assurance had access to the server, but not the department managers. The coordination effort was correspondingly high.
Using the new tool, however, it is not only possible to check the status quo of training courses. Hennig Arzneimittel also creates qualification profiles and assigns them to the relevant documents. The tool is also suitable for creating question catalogs or multiple-choice tasks for training courses. After successful processing, it automatically updates the employee’s qualification status in the qualification matrix.
"The next thing we want to do is digitize the change control management"
Hennig Arzneimittel has been using DMS and training management tool since July 2020. And is convinced of d.velop: “We found the collaboration to be both purposeful and cooperative. Together we have implemented a solution that makes our everyday work safer and more productive,” concludes Murawski. The next project is already ready to go. “Currently, controlled change management in our operation is still conducted on paper. In 2021, we want to computerize the Change Control Management with products of d.velop. And in doing so, take our digitization one step further.”
Would you like to learn more about our solutions?
Then take a look at our solution overview now