
Eimermacher group reduces time and sources of error when processing documents - Learn more about the success story
"Many documents, templates or files found themselves in our Windows folder system. This was not the ideal case. We wanted that to be better, more accessible, safer and faster. Where we used to have to browse through folders, we're now much faster. We now have more time for higher quality work. We used to have a lot of folders and needed a lot of head work. Now it's higher quality work."
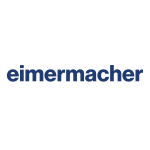
When the manufacturer and enthusiastic balloon pioneer Ferdinand Eimermacher met a tropical doctor friend in 1930, he could not have known that this meeting would be the breakthrough for Eimermacher’s company: The tropical doctor brought back highly effective natural balms from Peru, whose disinfecting and germ-killing effect was groundbreaking. Eimermacher used this effect for a new milking ointment that set a new standard for milk hygiene.
From this groundwork the Eimermacher Group evolved with seven companies and a wide range of goods in the fields of cosmetics, ointments, medical products, natural skin care as well as products for hygienic milk production in agriculture.
Today, the Eimermacher Group, a pharmaceutical and cosmetics producer with its headquarters in Nordwalde near Münster, employs around 230 people. The products find their way to customers in over 70 countries. Companies can be proud of such organic, healthy growth.
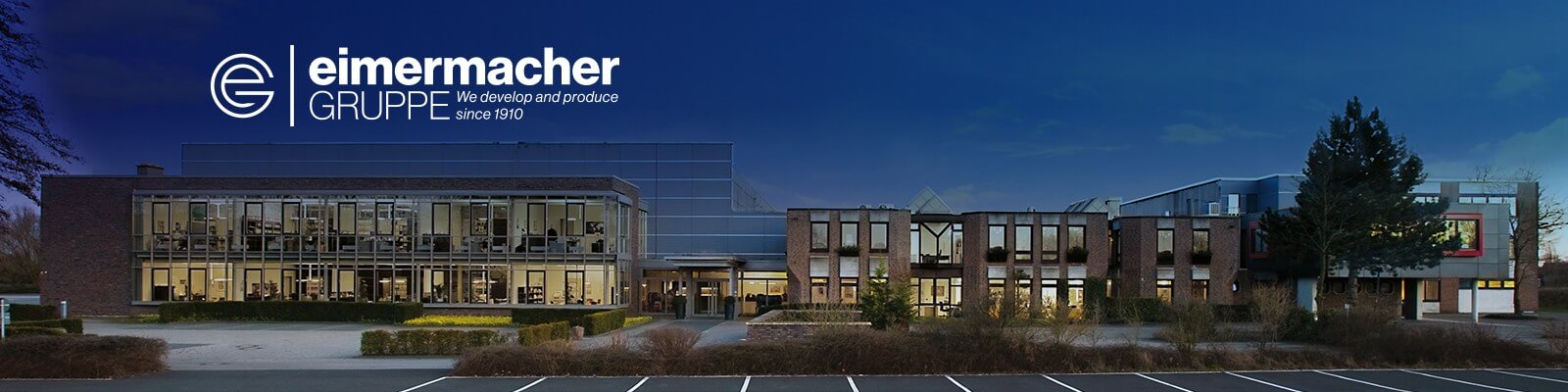
Paper-based processes cost time
Anyone who grows organically will have to reinvent parts of their organization at some point, as requirements outgrow previously tried-and-tested structures. This also happened at the Eimermacher Group. For example in the pane of invoices: “All receipts and documents relating to sales and purchasing were less and less suitable for tracking,” explains Conny Klemm, IT administrator at the Eimermacher Group, “and the process was taking longer and longer.”
The Eimermacher Group is not alone in this; paper-based processes are taking up time more and more time in growing companies. All the more so when something has to be searched for or tediously traced. For this reason, financial or supervisory authorities now also insist on electronic, audit-compliant archiving in many cases. Especially as part of accounting, searching for delivery notes, invoices or other documents is often particularly time-consuming and grueling.
“We had our documents in all sorts of variations,” says Stefanie Brüffer, project manager at Eimermacher Group, “a lot of it was signed by hand.” Klemm adds: “Many documents, templates or files found themselves in our Windows folder system. This was not the ideal case. We wanted that to be better, more accessible, safer and faster. We saw the need for action in order to remain legally able to act.”
In search of a partner for the digitization of business processes
With this need for action, in a first step, the Eimermacher Group turned to edoc solutions ag, a specialist for enterprise content management (ECM) and document management systems (DMS) for the digitalization of business processes. “It quickly became clear that the Eimermacher Group needed a flexible digitalization solution that offered many options for expansion,” says Frank Breyer, Project Manager at edoc solutions ag: “There was a lot of potential in the area of quality management alone. Example: The composition of pharmaceutical and medical preparations must be documented down to the smallest ingredient in many countries. This has so far been meticulously tracked by hand and Excel.”
One result of the initial discussions was that a specialist for GxP-compliant software for document and quality management had to be brought on board: Digital Life Sciences GmbH. Experts use the term “GxP” to refer to guidelines for good working practices in the pharmaceutical sector. “edoc solutions ag brought us on board to set up a digital QM manual as well as other QM processes, digital document control and the CAPA workflow,” explains Frank Laumann, Head of Services at Digital Life Sciences GmbH.
The ideal basis for these requirements is the dls | eQMS. On this basis, edoc solutions was able to digitize further business processes and divisions. The core system for this was set up within a few months. In the meantime, 100+ employees are working with the system.
Central digital business processes at the Eimermacher Group
With the dls | eQMS, the Eimermacher Group has developed a strong digital backbone consisting of these elements:
- Quality management (QM) with dls | eQMS as the central client
- Document Control with digital document circulation, creation, review, approval and release
- Controlled QM manual with over 600 valid regulations such as work and process instructions as well as manufacturing documents
- An independent document archive for commercial documents
- CAPA workflow for Corrective And Preventive Actions
- Reporting tool for open and completed training tasks
- Digital workflow for incoming invoices with automated connection to the Infor IGF financial accounting system as well as connection to the Infor Blending ERP system by edoc solutions
- Audit-compliant storage for documents
- Contract management for leasing, purchase and shareholder contracts
- Digital signature for internal use
- Possibility to develop customized tools
And this is how it works in the section of invoices, for example: “When an invoice arrives on paper, we scan it in,” explains Conny Klemm, “proofread it digitally, make a preliminary account assignment, forward it to the customer for verification, who then approves the invoice and ensures that the accounting department receives it. This ultimately clicks ‘Post’ and transmits the data to the accounting program.”
Current standards and SOPs always on the table
The automations not only save Eimermacher employees time, they also eliminate sources of error. This is particularly interesting in the field of quality management (QM). The dls | eQMS supports the Eimermacher Group in creating, correcting and releasing QM documents such as work instructions (SOP) or standards. There are no more local shadow copies and, via full text search, all employees with QM access can access the files that are important to them with just a few clicks. The tedious search through many Windows file folders is a thing of the past.
“The employees always have current standards or SOPs on the table,” says Klemm, “for our group of companies, we have an organizational chart in the QM system, everyone can click through and find their work area or that of their colleague. That has an advantage when onboarding new colleagues, so we don’t have to keep reinventing the wheel.”
If an employee is absent at short notice, a colleague from another office can take over seamlessly – in the virtual working environment of the dls | eQMS. Klemm: “And if you can operate a machine in production, you can also edit other production orders. We used to have a lot of folders and needed a lot of head work. Now it’s higher quality work.”
This works thanks to digitized training tasks. For example, if there is a new work instruction or a new machine is introduced, quality management can provide the relevant employees with new instructions and information via the system. Before they can tackle the new job, employees must answer comprehension questions and sign that they have taken note of the new information.
Annual folder bundles information on business partners at a glance
For the Eimermacher Group, digital documents not only mean less susceptibility to errors and quick retrieval, but also bundling of information in the right place at the right time. “The dls | eQMS also provides us with a history for each business partner,” explains Stefanie Brüffer, “this is an annual file containing all receipts, order confirmations, delivery bills, invoices, credit notes, letters and other information.” Klemm adds: “Where we used to have to leaf through folders, we are now much faster.”
This is also because there are fewer pitfalls due to the digital system. For example, the software automatically reminds employees to include mandatory information in documents – such as a customer’s name or a subject line. Klemm: “Letters that cannot be assigned to a customer or supplier are a major mishap. In the worst case they ended up in some Windows file folder and could only be found again with a lot of work. That’s history now.”
The digital workflows also automatically catch things that are implausible. Such as discrepancies between purchase orders, invoices and actual goods received. In the time before dls | eQMS and before edoc solutions, the Eimermacher Group’s incoming goods department, for example, collected all delivery bills in a folder. This folder had to be walked to Purchasing to verify that the delivery bill matched the invoice. “Now we compare the invoice with what was actually delivered and ordered,” Klemm said. This is achieved, for example, by the incoming goods department counting cartons or weighing incoming raw materials, entering the information into the system and sending it automatically to purchasing. Klemm: “That saves an incredible amount of working time. Because all the information is in one system at a glance.”
Economic advantages
The Eimermacher Group benefits from these economic advantages, among others:
- Save time when researching and editing documents
- Automatic versioning: Time savings through document control – everyone works on the same document, no more version ping-pong by e-mail
- Fewer errors in document processing due to mandatory entries etc.
- Save time with digital text recognition and preliminary checks of invoice amounts and other data from the system
- Faster processing of incoming invoices – more opportunities to draw discounts
- Easily meet validation requirements through standards such as ISO 9001
- Make remote audits possible
- Employees always have up-to-date work instructions on the table
- All Group companies have access to the latest standards
- More time for higher quality work
Would you like to learn more about our solutions?
Get a holistic overview of our versatile digitization solutions now