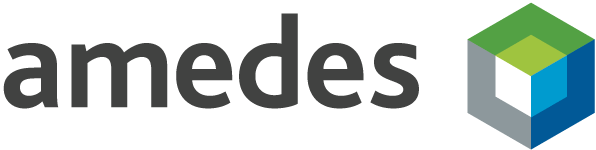
Digital QM and training management for laboratory network amedes group
"Prior to 2016, we did have an electronic document routing system in place, but it was all not as clean and performant as it should have been. For example, we missed a good overview of which employee is trained to what extent. That's what we have today thanks to Digital Life Sciences. This is important, for example, for an external audit. With the old system, we still had to do many things manually. With Digital Life Sciences' eQMS solution, quality and speed have taken a leap upward."
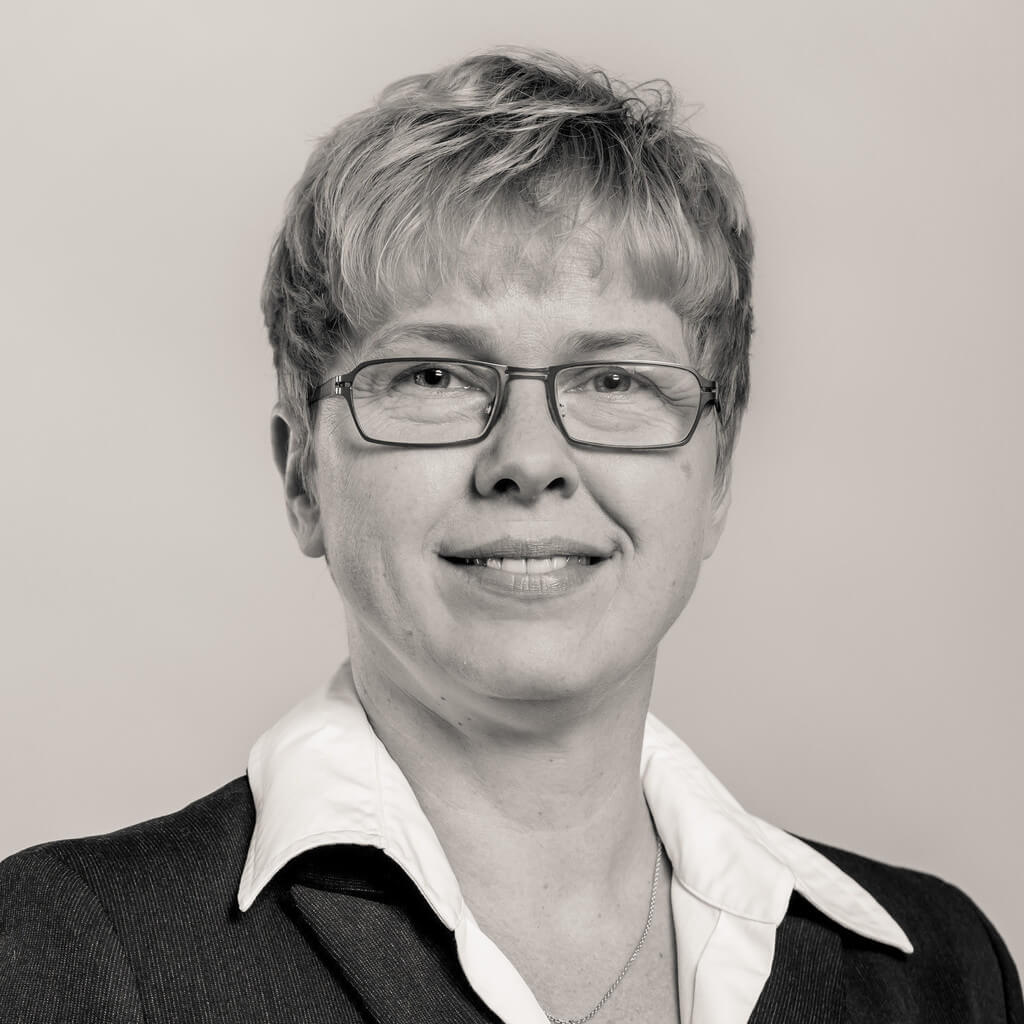
It’s one thing to have to retrieve thousands of documents every day, check them and keep track of which employees have already read them and which still need to catch up. But it’s quite another thing to be responsible for this in the medical sector.
The amedes group does just that. It provides medical-diagnostic services for patients, practicing physicians and clinics. To this end, amedes has over 4000 employees at more than 90 locations. Across Germany, the group serves around 40 clinics, and specially trained employees edit more than 400,000 laboratory analyses every day. In this way, amedes specialists treat over 450,000 patients a year.
It goes without saying that all the steps have to be perfect and flawless. A key factor for this high quality standard is the meticulous maintenance of quality management manuals and documents. Fortunate are those who can use a strong and easy-to-operate digital quality management system for this purpose.
“Before 2016, we did have an electronic system in place to manage documents,” describes Yvonne Kraska, head of QM at the amedes group, “but none of that was as clean or as performant as it should have been.” For example, the company lacked a clear real-time overview of which employee had already read which document or work instruction and also acknowledged this by signature.
It also lacked the ability to assign documents to specific employees. Some sites could not be trained digitally and therefore used a paper process rather than a digital reading confirmation. “After reviewing documents, some employees were still able to make changes with the old system,” Ms. Kraska describes, “We wanted that to be different.”
Transparency and overview in quality management
In search of an alternative, the amedes group came across the Document Control module from Digital Life Sciences GmbH. “We looked at a lot of systems,” said Yvonne Kraska, “and Digital Life Sciences made a difference like night and day. Many alternatives were not comparable at all. Of course, we also had to make some sacrifices and decide which system we wanted to live with. After all, a single system cannot take everything into account from the very beginning. It was then that we said, in perspective, we want to continue working with Digital Life Sciences.”
Forms, work instructions, quality manuals, training documents, and customer invoices: The amedes group and Digital Life Sciences GmbH jointly transferred these document types to the new document management system in a very short time. Documents from the sections of quality management, manuals and training documents were initially given priority. “One example,” says Frank Laumann, Director Services at Digital Life Sciences GmbH, “is the work instruction on hygienic hand washing. If you maintain 40 sites, you must maintain this instruction 40 times. Today, the amedes group has a central digital document that only needs to be managed once.”
If the central digital document is changed, the changes are available almost simultaneously at all locations. And Yvonne Kraska can check virtually in real time which employee has already taken note of and signed the updated document. The new digital workflow with digital document control also saves steps and paper when creating new documents.
In 2017-2018, various individual contracts, corporate legal documents, master agreements, patents, trademarks and supplier agreements were added.
Digital document control process with several participants
Write or create, review and sign documents: “With the digital Document Control, the amedes group now has significant time savings,” describes Frank Laumann, “if only because tasks and papers come in via e-mail and can be digitally signed immediately.” The amedes group currently uses digital signatures only for internal purposes, so a comparatively simple legitimization of users through their login into the company’s own system is sufficient.
Many employees work together to create documents. As with many processes in business, there is a bottleneck: “Typically that’s the reviewers,” says Ms Kraska, “which in most cases is one of our employed doctors, and they’re extremely busy.” So far, so usual, so hardly avoidable. But the new software saves the amedes group a lot of extra resources that used to be lost between the individual process steps.
It used to be called: Write, print, transport. Review. Then sign. Transport again. Copy. File. Archive. At each step of the process, employees could lose sight of the issue, misfile a folder, bring other tasks forward. In the worst case, this could cost the company days. “Today, ideally, it takes us 30 minutes to have a new document reviewed and circulated,” describes Yvonne Kraska. “We save the running around, the running after, the copying, the manual filing and archiving. The system also automatically reminds colleagues of any expiring deadlines.”
Digital proofs of training: legally secure and traceable
Scrupulously following work instructions is a key factor for success, especially in the medical sector. After all, no patient wants to receive false test results. “Does an object need to be colored blue or red? A bottle to be placed on the left or right? What does a colleague do when a device reports an error?” Yvonne Kraska remembers: “In the past, there were signature lists on paper, sometimes even stapled to certain documents. Changes were marked, sometimes had to be printedout, because it was not possible to go paperless everywhere. And the acknowledgement was confirmed manually.”
This manual process meant a lot of work due to frequent checks. This additional effort is now saved by the entire group. In most cases, electronic documents are also acknowledged electronically, and the system logs the signatures. Ms. Kraska: “I can see in the system what’s happening. From all over the world, if I want, I can see who has already signed and who still needs to acknowledge a document.” The reading confirmation is GxP compliant and traceable. “That’s important,” Ms. Kraska said, “for an external audit, for example.”
The amedes group has access to this information, among others:
- Which document hangs in which correction status?
- Which work instruction applies at which site?
- What is the state of versioning of certain documents?
- Which documents are assigned to which employee?
The information can also be accessed on the move, for example via smartphone or tablet. For the laboratory network, the time savings in particular are a decisive advantage. Ms. Kraska: “In the past, it felt like we were still working on foot a lot.”
Central digital business processes of the amedes group with digital Document Control
- Creation, review, revision and archiving of documents
- Follow-up of trainings and acknowledgement of e.g. work instructions
- Management and distribution of QM manuals at all sites
- Output of e.g. work instructions to the corresponding workstations
- Archiving of customer invoices
- Management of contracts (primarily internal)
- Uniform specification of document templates and layouts
Yvonne Kraska’s conclusion: “With the old system, we still had to do many things manually. With the eQMS solution from Digital Life Sciences GmbH and the d.velop documents platform from d.velop AG, quality and speed have taken a leap upward.”
Would you like to learn more about our solutions?
Then take a look at our solutions overview now