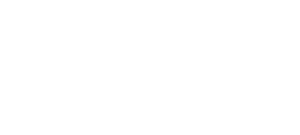
zwissTEX GmbH accelerates circulation of quality management documents to one day
"As an automotive supplier, we really do have very extensive documentation obligations in quality management. In the past, such an amended regulation took a good week to circulate. We have looked at many solutions to optimize processes. But when we saw what the digitalization solutions from Digital Life Sciences can do, we looked no further. Everything is now transparently documented, versioned, archived and traceable"
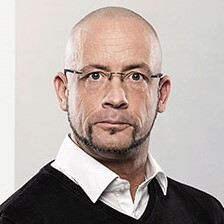
zwissTEX GmbH
In the cars of tomorrow, there will be no one at the wheel who doesn’t want to. And when the car drives itself, the interior of the vehicle draws all the more attention to itself. The high-tech textile manufacturer zwissTEX is prepared for this: with innovative textiles that can replace complete design and construction concepts.
The history of zwissTEX goes back to the year 1828. Even back then, a forerunner of the GmbH recognised the signs of the times and produced textiles from natural fibres. Over the decades, zwissTEX has reinvented itself and its product catalog again and again, and today the company is a sought-after partner with its high-tech textiles.
The headquarters of the company is located in Gerstetten between Stuttgart and Munich. With new composite materials, warp-knitted and spacer fabrics and many other products, zwissTEX supplies not only the automotive, clothing and medical technology industries, but also the aviation and ultra-lightweight construction sectors.
But working in an industry that is very close to the automotive sector is not only exciting and inspiring. It must also comply with a comprehensive obligation to document work steps. Quality management (QM) is also a decisive factor, and here every vehicle manufacturer has its own specific requirements that suppliers such as zwissTEX must comply with.
zwissTEX initially relied on paper, Word and Excel for quality management
“As an automotive supplier, we really do have very extensive documentation obligations in quality management,” says Mark Seewald, Head of Integrated Management at zwissTEX. Quality management comprises methods with alowing companies to combine requirements for quality, environmental protection, occupational health and safety, safety and others in a uniform structure. The workers in production must have access to the current papers at all times and comply with the regulations.
ZwissTEX has long relied on paper documents as well as Word and Excel to handle the extensive tasks in quality management. For example, at least three people must sign regulations at zwissTEX before they can be enacted. “So an employee created a regulation,” describes Mark Seewald, “made a copy and ran all over the site to circulate the paper.”
When a specification for production was changed, this specification on paper had to be communicated to, among others, the area manager and the shift supervisor before it arrived at the production department. “In the past, such an amended specification took a good week to circulate,” says Seewald. Up to 900 specifications on paper circulate in the company, and if something changed, the analogous things took their course. This kept employees busy for many hours a week.
“zwissTEX GmbH had previously used a file system with Word documents,” recalls John Stender, project manager at Digital Life Sciences GmbH, the Competence Center of d.velop AG for quality management and partner of edoc solutions ag. ZwissTEX was not alone in this: “Many companies use similar structures like folders with documents as well as Excel lists to track versions and validity.”
Wanted: an electronic quality management system
The time came when zwissTEX’s previous workload with paper documents in the area of quality management became too much. After all, it took time to release and place documents and keep them up to date. Consequently, the company looked for an alternative – a digital quality management system.
“We looked at many solutions to optimize processes,” says Mark Seewald, “but when we saw what the digitalization solutions from Digital Life Sciences could do, we didn’t look any further.” The highlight: zwissTEX was already using d.velop documents (formerly d.3ecm). The company had been using the system by d.velop AG for half a year for an electronic processing of incoming invoices in SAP, digital supplier and customer folders as well as for legally compliant e-mail archiving. Using these tools, zwissTEX had already digitally optimized workflows and processes, and reduced research and processing times. This leaves the employees more time for the actual, creative work.
Digital base came from edoc solutions ag
Here, edoc solutions ag from Weilerswist as the largest d.velop documents (formerly d.3ecm) partner of d.velop AG had already laid the foundation. in 2018, edoc implemented d.velop documents (formerly d.3ecm) at zwissTEX. “A befriended company recommended us and during the evaluation process at zwissTEX we were able to convince them with our ECM portfolio,” recalls Alexander Ferrauti, Account Manager at edoc. Until 2018, many processes at zwissTEX still ran with paper documents, and with the introduction of d.velop documents (formerly d.3ecm), documents such as quotations, orders or receipts were now automatically archived in the customer or supplier files in d.velop documents (formerly d.3ecm). Alexander Ferrauti: “After manual storage, automatic document archiving from the SAP system or the scanning process, the system automatically assigns the documents to the digital process.”
As a result, d.velop documents (formerly d.3ecm) was one of the first steps taken by zwissTEX as part of its digitalization strategy. “It was not only about making documents digitally accessible”, describes Ferrauti, “but also about the first digital workflows and processes. Such as the digital incoming invoice.” Since d.velop documents (formerly d.3ecm) was set up by edoc solutions ag, zwissTEX employees have always been able to track where documents are currently located. Invoices could be checked or approved immediately and at any time, even while on the road, as could other documents.
Starting signal for the digital quality management of Digital Life Sciences GmbH
After the familiarization phase with d.velop documents (formerly d.3ecm), zwissTEX commissioned edoc solutions ag to expand the existing d.velop documents (formerly d.3ecm). The target: Employees should be able to edit, view and update QM documents digitally. “We were able to build our interface very well on the ECM d.velop documents (formerly d.3ecm), which allows us to respond to the requirements in the section of quality management,” describes John Stender.
The joint project to set up and adapt the system for digital quality management started in January 2019. The solution only had to be slightly adapted to the needs of zwissTEX. In the medical industry, for example, companies must follow extensive guidelines known as “GxP”. “zwissTEX is not a classic GxP customer”, Stender describes, “but the requirements are similar, because zwissTEX has based its quality management on GxP standards.”
In their daily work, zwissTEX employees have to create, update and release many digital QM documents, some of them with digital signatures. The introduction of the digital document management was only the first step. In contrast to working with Word and Excel, the quality management solutions from Digital Life Sciences offer a structure that the workflow can use as a guide. Employees are given different user roles only granting them access to the documents and sections they really need. This not only ensures order and clarity, it also dries up a possible source of error.
Runtimes reduced from one week to one day
Moreover, each employee has an individual overview of all tasks, deadlines and documents. “At the beginning, we initially mapped our organizational chart in d.velop documents (formerly d.3ecm),” Seewald recalls. Users could then assign tasks, such as checking or approving a document or even working through a root cause analysis. The tasks receive deadlines and key dates, the persons in charge receive a notification via Microsoft Outlook. If the validity of a document expires, a person in charge of QM receives a message.
From project start in January 2019, it took only six months to go live. Seewald: “We have also set up an additional employee qualification module to record which colleague must be trained on which documents and which trainings have already taken place.”
The new software also makes it much easier to keep track of documents and deadlines even in the heat of the day. Accordingly, the user is automatically reminded about the expiry of a possible deadline. Access to the relevant documents is also faster and more convenient. Nobody has to scroll through folders anymore – with the full-text search, the decisive document is only one click away.
Seewald: “In the past, for example, new specifications for production took a week for the circulation of documents. With digital quality management, this is done within a day, in rare cases it takes two days.” Since its introduction, 350 employees now work with the digital quality management system, including the employees at the zwissTEX site in Mexico.
This is how digital quality management works at zwissTEX
ZwissTEX has divided its digital quality management into five process groups:
- Document management
- Change Control (change management)
- CAPA (Corrective And Preventive Actions)
- Deviation Control (deviation management)
- Employee qualification
“We decided to go with d.velop”, says Seewald, “because all five components and solutions we needed were already available in one software. The software is also expandable, for example for contract management.” In July 2019, shortly after the document management system was set up, zwissTEX introduced digital change management (change control) based on d.velop documents (formerly d.3ecm).
The reason: Before the introduction, the zwissTEX employees had their hands full managing the changes. Some change requests came by e-mail, some by call-in between the coffee kitchen and the desk, and some even by Post-It. Seewald: “So we needed a digitally controlled change management system, also to meet the requirements of the International Automobile Task Force (IATF).”
Example: A zwissTEX customer changes his recurring order. He now needs yellow instead of red parts. zwissTEX must therefore produce yellow parts in future – a change that affects many departments, from production and invoicing to printing delivery notes and labels.
“With d.velop documents (formerly d.3ecm), our employees maintain an overview,” explains Seewald, “and we avoid frictional losses.” Digital change management creates a task list for all involved or responsible employees and keeps track of the processing. Employees receive a message via Outlook when new tasks are due or they have to act in the process. For example, production employees can upload a photo of the first yellow parts to confirm that they are now producing yellow parts, thus meeting the zwissTEX customer’s change requests.
The other areas of quality management, such as the management of corrective and preventive actions, work in a similar way. After all, it is not enough to simply communicate a change request. Employees must also translate this change request into measures and keep track of whether these measures have been processed. And in due time and form. Last but not least, any complaints must be tracked down and processed using deviation management.
Seewald: “A big compliment to Jacqueline Gollan, quality manager at zwissTEX. The rapid implementation of an electronic quality management system would not have been possible without her; she was the driving force behind the project”
"We've collected all the specifications on paper"
“The great advantage of digital quality management,” says John Stender, “is not only the direct access to documents, deadlines and tasks, but above all the fact that it is up-to-date. Documents are always up to date, which is a great added value for the production staff. They no longer have to worry about whether they have the correct and current instructions.”
This way, zwissTEX eliminates a lot of friction losses. And a lot of paper. “We have collected all specifications on paper”, emphasizes Mark Seewald, “in the entire production there are no more specifications on paper.” All process descriptions, work instructions, procedural instructions and the complete QM department are now digitalized. Seewald: “Everything is now transparently documented, versioned, archived and traceable.”
Would you like to learn more about our solutions?
Then take a look at our solution overview now