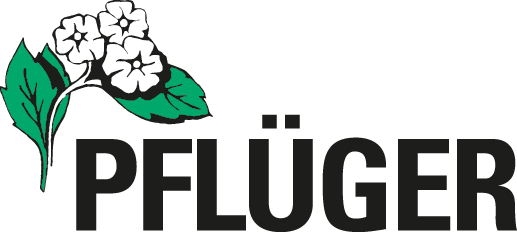
Homöopathisches Laboratorium Alexander Pflüger GmbH design digital processes themselves
“Years ago, we used to track the status of documents such as work instructions, employee qualification records and batch reports using an Access database or on paper. However, it was tedious to keep the documents up to date and to manage them in an audit-compliant manner. In 2012, we switched to the digital document management of Digital Life Sciences, which was a quantum leap. Today we can create, find, edit and coordinate documents much faster. This saves working time and costs.“
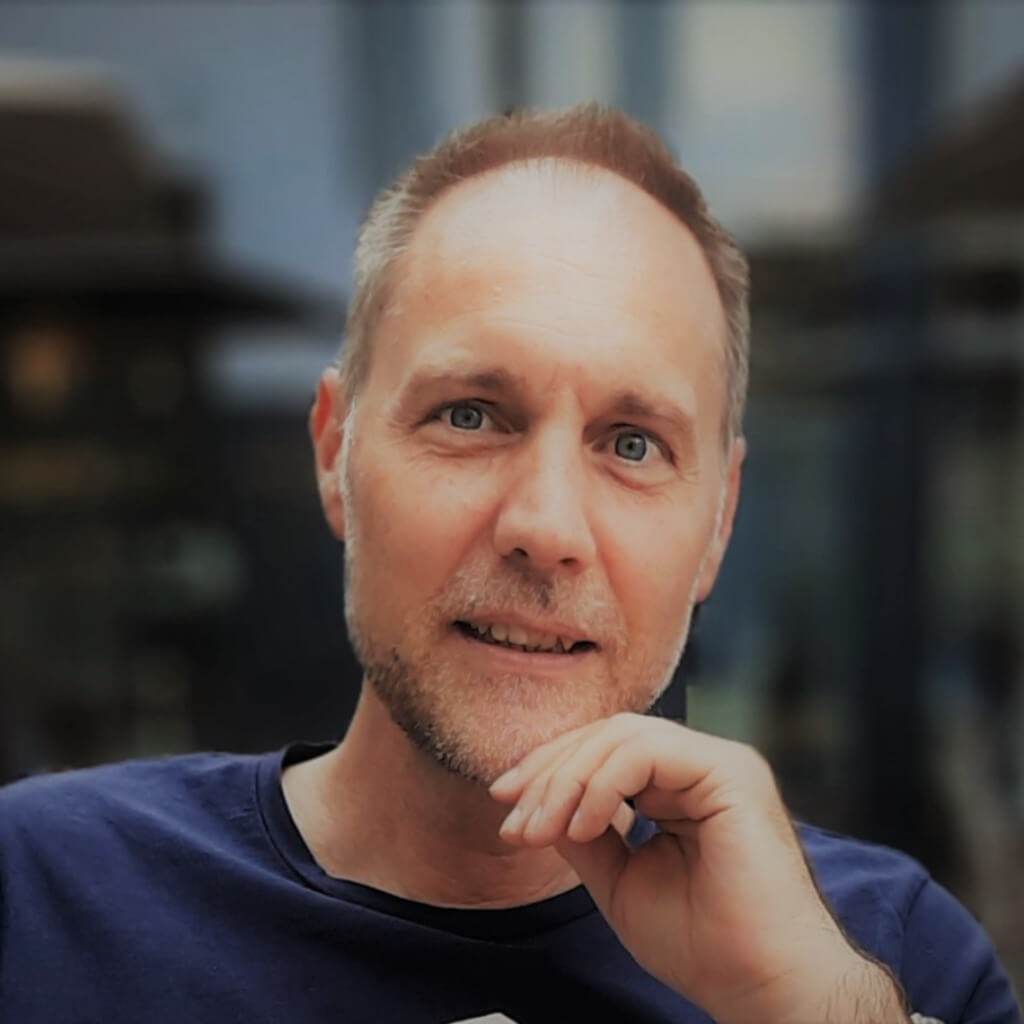
Strict regulations from the HAB (German: ‘Homöopathisches Arzneibuch’, Homeopathic Pharmacopoeia) apply to the production of homeopathic medicines. Therefore, the approximately 130 employees of Pflüger GmbH in Rheda-Wiedenbrück in North Rhine-Westphalia pay meticulous attention to the various work instructions and process manuals during production. A large number of work steps are prescribed for the approximately 350 medicines that Pflüger has in its range.
The GmbH relies on seamless quality assurance (QA). A plethora of QA documents must therefore be created, periodically monitored and passed on to the respective employees for training. Years ago, Pflüger employees used a hybrid solution of Access database and paper-based processes, for example, to keep track of who had already received which instruction.
“At that time, each department had its own paper file,” describes Björn Boxhammer, Head of IT and Quality Assurance at Pflüger GmbH, “and we in Quality Assurance had to exchange the relevant documents by hand when there were new versions. Moreover, we had to keep track of when the document was read.”
Years ago, such manual tracking and organization may have been feasible. However, many procedures, processes and guidelines have now become more complex and specific. “That’s where software helps to keep track,” Boxhammer sums up. After the consistently good experiences in the process of the archiving solution for quality-relevant documents, Pflüger GmbH switched to the newly established Life Science Client of Digital Life Sciences.
Get signatures for QA documents faster
“Especially for the management and training of QA relevant documents, a paper-based process is a lot of work,” says Frank Laumann, Head of Services at Digital Life Sciences. “A quality management manual with all its procedures, work instructions and forms must be signed by several people. A digital process has an accelerating effect here, especially if the documents are to be made accessible to many employees.”
One focus of Digital Life Sciences is on software and services for companies in the pharmaceutical environment. “Among other things, the relevant know-how was crucial for us,” says Boxhammer, “and the sense of proportion with which Life Sciences approached the processes. That meant a high degree of certainty for us.”
As a basis for digital document control, Digital Life Sciences uses the document management system d.velop documents (formerly d.3ecm). The software is powerful: Over the years, Pflüger GmbH has accumulated almost two million documents in the system, both GxP-relevant documents such as process and work instructions and proof of employee qualifications, batch reports, active ingredient documentation, but also commercial documents such as contracts, e‑mails, invoices and many more.
Design digital processes yourself
The system now digitally implements many processes so that no quality assurance employee has to manually update documents in various folders. An example: Preparation of documents such as procedural instructions or mandatory pharmaceutical texts, but also marketing texts for the print sector. “This can be done wonderfully with the system,” says Björn Boxhammer, “employees enter their draft texts centrally and are forwarded to colleagues for review and approval using workflow. Thanks to digital document control, everyone always works on the same, constantly up-to-date version.”
Among others, Pflüger GmbH has meanwhile implemented these processes with the digital document control of Digital Life Sciences:
- Contract Management
- Incoming invoice processing with approval process
- Continuous updating and provision of quality management documents, procedural instructions, such as MOP (Master Operating Procedure) and SOP documents (Standard Operating Procedure)
- Organization of packaging designs for folding boxes, labels and inserts
- Various marketing processes with approval of print templates and advertising material
- Management of mandatory pharmaceutical texts
- Archiving of manufacturing documentation and sales documents
- E‑mail archiving
The document control process is rounded off with the fully integrated Training Management module. This module controls which updated documents have already been read by which employees: if, for example, there is a new work instruction, the system automatically sends a read and understood training to the employees concerned and places it in the employee’s task mailbox.
Automatic reminder of expiring deadlines and other benefits
For contracts, Deadline Management from the Contract Management module automatically reminds you when deadlines are about to expire. “This not only saves me working time, but also any additional costs that may be incurred, in the event of missed notice periods,” says Boxhammer. The system displays folder links and associated documents so that, for example, invoices, contracts or complaints for a supplier are displayed in an overview. Employees can find documents with the full-text search function and a few search terms, just as if they were using an Internet search engine.
One of the latest implemented projects with existing software is digital incoming invoice verification. Originally, most invoices were received as paper, but later more and more were also received as PDFs. Employees printed the PDFs, applied the account assignment stamp to each invoice, and scanned the invoices back in with expanded information. This made for some sources of error, but most importantly, the paper invoices were stuck too long in the verification cycle that was distributed through the in-house mail.
Digital incoming invoice automatically recognizes data
After implementing the digital incoming invoice, the system now automatically recognizes incoming invoices and digitally records information such as supplier, invoice number, total amount and invoice date. After recognition, the invoices run through the workflow for factual verification and entry of item data. If information is inconclusive or contradictory, the system indicates this to a responsible person. The system then sends the invoice on for approval and, in the final workflow step, to financial accounting for release. “This puts an end to tiresome enquiries about which cost center or which G/L account an invoice has to be posted to,” says Boxhammer. Provided that everything is in order, all recorded data is transferred to the database of the IGF accounting system connected via interface.
Furthermore, document control allows the employees of Pflüger GmbH to create, change and design digital processes themselves. “With d.velop documents (formerly d.3ecm) we have a platform for many entrepreneurial issues, which all grow out of quality thinking. The Digital Life Sciences promises nothing that is not also kept. Today we can create, find, edit and coordinate documents much faster. This saves working time and costs.” I wouldn’t want to miss this anymore, it’s really very good.”
Would you like to learn more about our solutions?
Then look at our suitable solutions now.