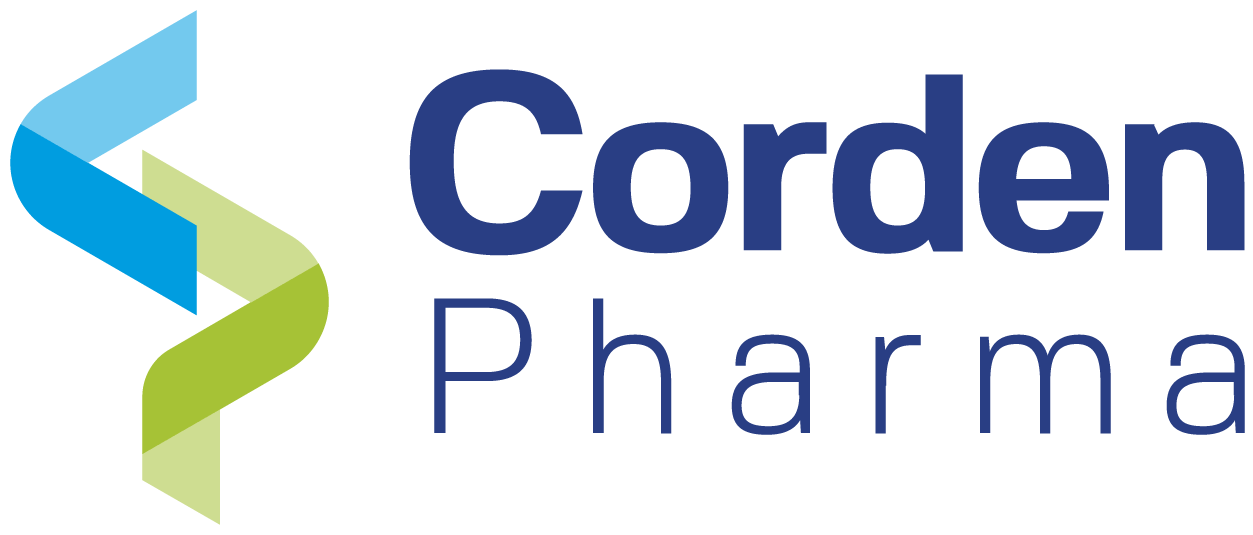
Corden Pharma speeds up processes by 20 percent with digital document control
"Digital Life Sciences has helped us to make our paper-based processes more digital. In the past, we mainly printed out a lot of things, stamped them, signed them and transacted them on paper or with office documents. Some things had to be kept in hardcopy form for years. Today, we work with real digital documents that we can distribute with just a few clicks, regardless of whether the employees in question are currently working at home or somewhere else. Processes have become at least 20 percent faster."
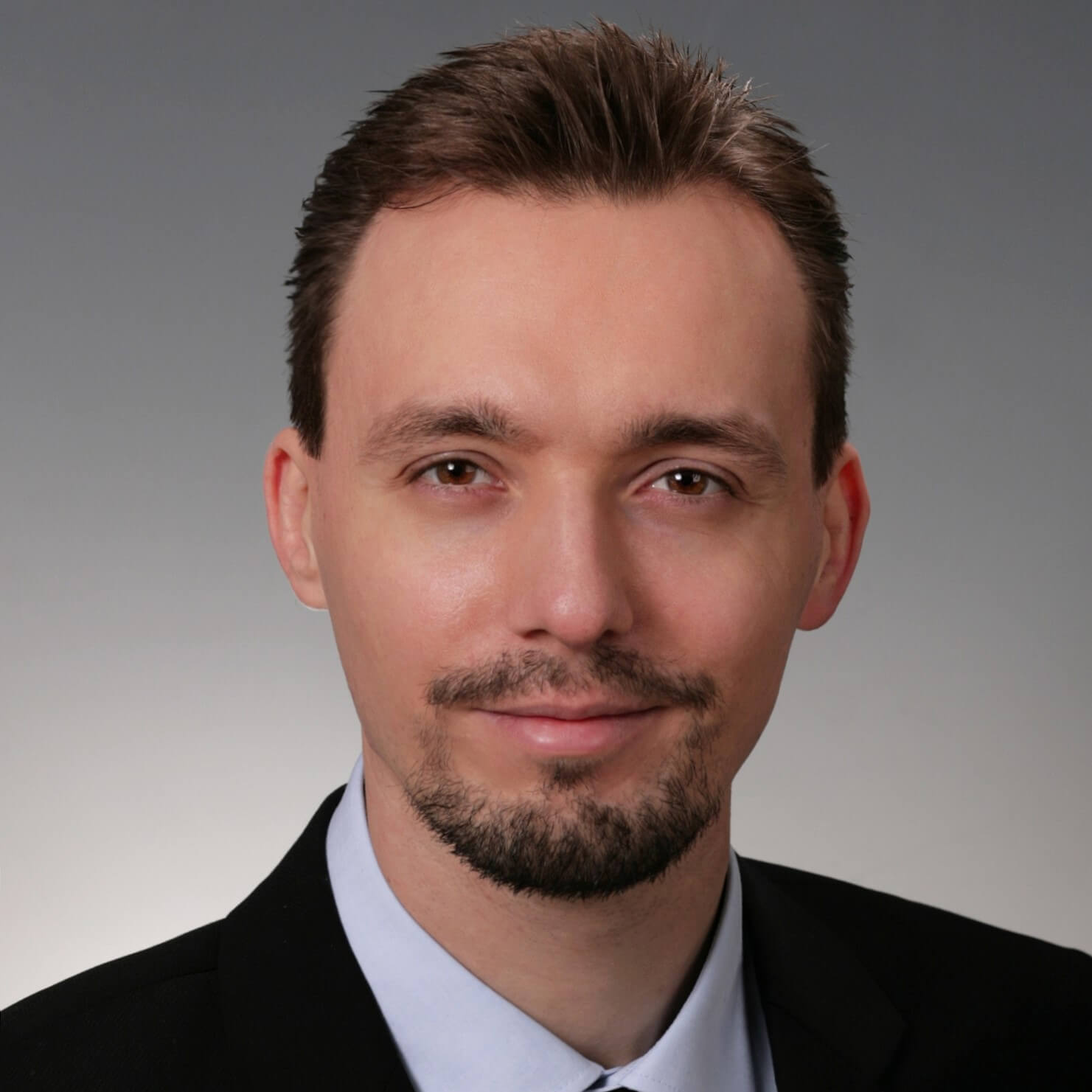
Painkillers, insulin, vaccines and much more: The pharmaceutical industry is a supporting pillar of the healthcare system. In Germany alone, more than 500 pharmaceutical companies manufactured drugs and pharmaceutical products worth around 31 billion euros in 2020. Companies like Corden Pharma Switzerland LLC. As part of Corden Pharma International, with eight closely cooperating sites worldwide, it is a major provider of active ingredients and services in the areas of development as well as manufacturing of active ingredients for pharmaceuticals (CDMO, Contract Development & Manufacturing).
In addition to economic responsibility, the pharmaceutical industry feels social responsibility. Therefore, there are extensive regulations, rules, guidelines. Many of these are known under the key term “GxP” as guidelines for good work practices. “In the pharmaceutical sector there is generally a very strong emphasis on documenting processes. This also applies to the documentation of manufacturing processes”, describes Arne Cadenbach, Project Manager at Digital Life Sciences GmbH.
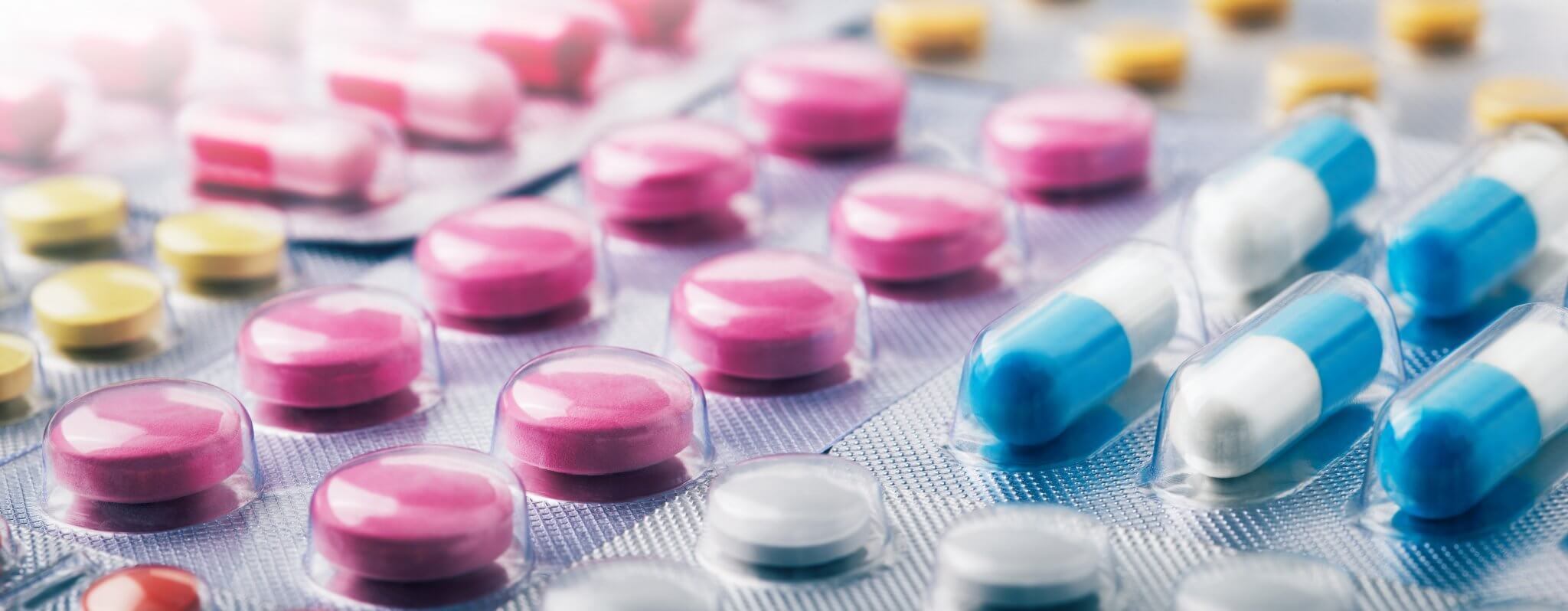
Meticulous documentation via hardcopy and office documents
In past years, Corden Pharma Switzerland LLC relied on a meticulous process involving hardcopy and office documents. However, some operating or manufacturing regulations (BVO) turn out to be several hundred pages long. In addition, Standard Operating Procedures (SOP) were created, corrected, released, printed and distributed to the appropriate employees. They then had to sign a training record to confirm that they had read and internalized the new regulations.
“That’s where we used Excel spreadsheets, among other things, to keep track of who was trained and when, with training records as proof. That was a lot of work for quality management”, says Witali Blum, Qualification Expert at Corden Pharma, “if a work instruction changed, a new version was produced, and the whole circulation through manufacturing, revision, release, distribution and training had to be done again.”
This meant a lot of work for the Corden Pharma staff. Anyone who has had to discuss and agree on a long office document with many employees via email knows this. “Especially in the home office, it can be even more difficult to keep track of emails with multiple file versions if I have to merge the versions manually”, says Arne Cadenbach.
Main objective: Improve training management and training
The good news: Such activities are well suited for digital document control. A software application manages the documents, keeps those involved in touch and records in metadata who made which change, release, or signature and when.
So in 2019, Corden Pharma Switzerland LLC set out to find a digital document control provider. “Initially, the main goal was to improve training,” recalls Witali Blum, “and Digital Life Sciences was convincing from the beginning. At first, digital document management was just an accessory, but that has gradually moved further and further to the front.”
The installation of the digital document control system was completed in one day; the data migration and software validation took considerably more time. Corden Pharma went live with Digital Life Sciences’ digital document control system in mid-2020. Blum: “We benefited from the experience that Digital Life Sciences has in validating software.”
It took a while for all employees to get used to the new procedures. Corden Pharma and Digital Life Sciences use the Key User Model to train employees. A few selected users receive intensive one-day training and pass on the information within the company. The administrators were familiarized with their tasks separately at a total of two training sessions.
Key benefits of digital document control at Corden Pharma
Right at the beginning of the setup process, it becomes clear what the scope of the new software is. Processes can run faster and more reliably, employees are relieved and have more working time free for other important tasks. Corden Pharma Switzerland LLC is now mapping these key points with the digitalization solutions from Digital Life Sciences, including document control:
- Production, revision of work instructions, Standard Operating Procedures (SOP) and other documents such as validation documents, specifications, description of production processes, documentation of test methods and many more
- Training Management – Organisation and tracking of employee qualification and training. For this, Corden Pharma uses electronic signature and automatic delivery of training tasks to the DMS mailbox of the participants: Once a new version of a training material is completed, it automatically lands in the task inbox of those concerned. This also applies to safety training
- Archiving of documents
- Release processes with electronic signature
- Controlled, traceable, up-to-date distribution and mailing of documents – instead of sometimes waiting days for paper mail to arrive
- Meticulous documentation of processes such as production, release and revision of documents, also to the satisfaction of pharmaceutical customers
- Ever up-to-date documents without big workload – the hunt for outdated versions is over
“Our work simply runs faster”, describes Witali Blum, “one example: In the past, when we needed a physical signature, it took time if the person was working from home or on vacation at that time. Today, they just get the document automatically into their digital task mailbox for release.” For the legitimation of the digital signature Corden Pharma uses the Windows user account. This ensures the authenticity of the signature for internal processes. Also many of Corden Pharma’s customers, who require some signatures in manufacturing or processing procedures, for example, agree with this process.
"The human error has become smaller"
“The traceability has simply gotten better”, Blum says, “and the digital processes have reduced human error in tracking versions that are in circulation, for example. The dls | eQMS has done away with that in one fell swoop, we’ve become faster and safer, and a lot of tedious work steps have been eliminated.”
On the business side, Corden Pharma also registers a financial benefit. And the faster and safer processes have freed up working time, which in turn benefits other areas or activities. Last but not least, paper consumption has also dropped – by half, as Blum notes. His conclusion: “Processes have become at least 20 percent faster.”
Would you like to learn more about our solutions?
Then take a look at our solutions overview now