
"We strive for sustainable growth"
"With its dls | eQMS, Digital Life Sciences GmbH is helping us to strategically develop our QMS and map electronic solutions / workflows in line with GMP and ISO requirements. Currently, the modules “Document Control”, “Training Management”, “Deviation Control” and “CAPA” have been implemented and the ERP system has been integrated on the interface side in order to be able to use the existing process information across systems. We are already looking forward to many exciting future projects thanks to the wide range of possibilities and the constant expansion of functions in dls | eQMS. Whether for the introduction of further document types or new modules, in order to be able to successfully further increase our efficiency and make our documentation more digital, traceable and centralized."
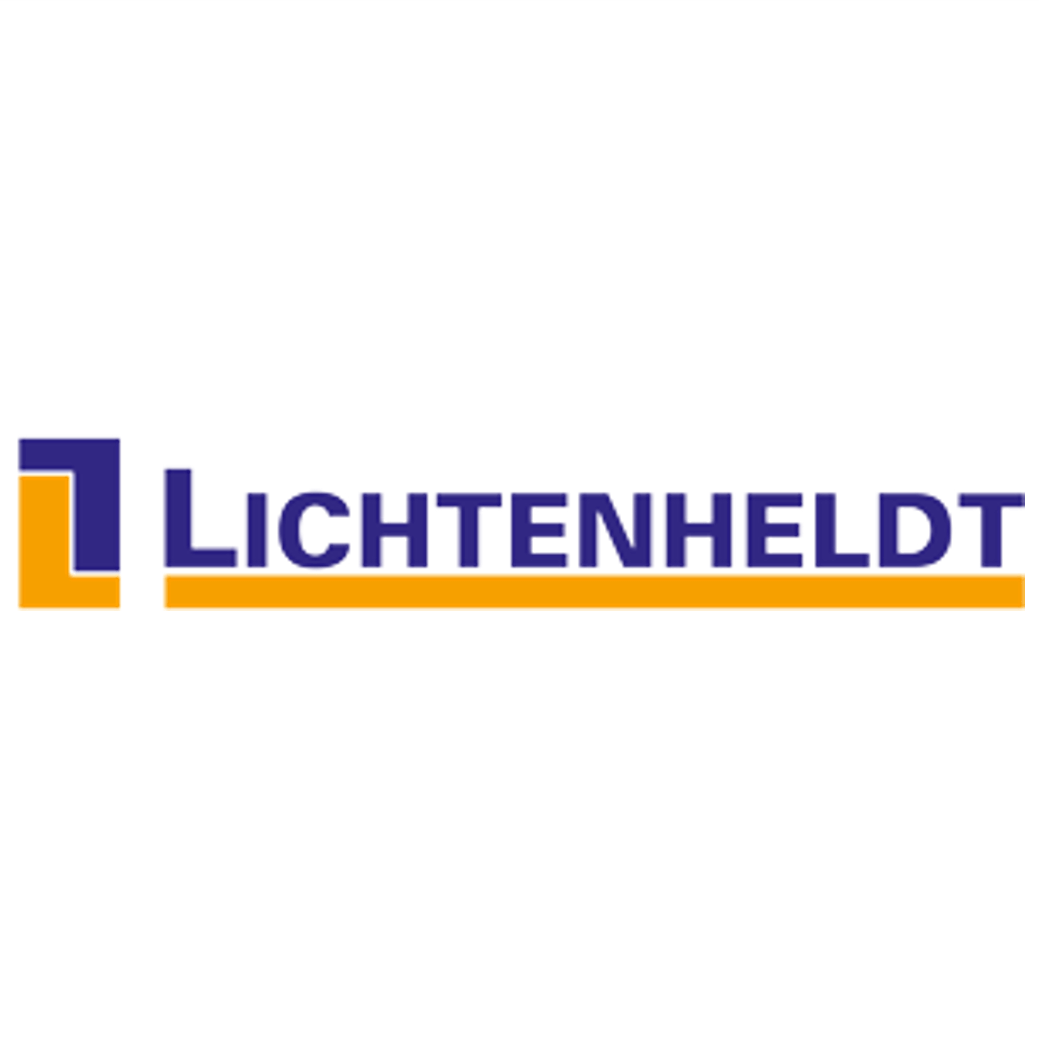
Goodbye paper printouts: Pharmaceutical manufacturer Lichtenheldt is digitizing its document management with the d.3 eQMS system from Digital Life Sciences GmbH. Why the company not only strengthens environmental protection, but also saves time and money.
J. N. Lichtenheldt would have been amazed: 276 years after he founded the pharmaceutical company Lichtenheldt in 1745, the company is one of the pioneers in the development and production of liquid and semi-solid pharmaceutical and medical products. With around 250 employees, the plant fills and packages more than six million liters a year in over 30 million individual containers. The task is to keep track of over 150 recipes. And much more: Standard Operating Procedures (SOP), work instructions that describe work processes in such detail that there is no room for interpretation for users.
A mammoth task that demanded a lot of energy and expense from Lichtenheldt in the past because it was still rooted in the analog world. “We wrote new work instructions on the computer, then printed them out with attachments, obtained signatures from those responsible, scanned documents back in and documented all processes in Excel lists,” recalls Marcel Rau, IT application at Lichtenheldt. This not only cost time, but also resources such as paper and printer toner. Additional pressure has come from the supply chain, where more and more participants want digitalization in quality management. “We strive for permanent improvement and sustainable growth so that our company can survive in an ever-changing business world. That’s why we decided to digitalize the SOP management.”
The d.3 eQMS system of Digital Life Sciences GmbH makes paper superfluous and accelerates work processes
In order to move away from paper and transfer quality management to the digital world, Lichtenheldt has installed a new ERP system and introduced the Digital Life Sciences document and quality management system. The basis of the dls | eQMS is a holistic ECM/DMS system, which can be modularly extended by further d.velop products for classification, structuring, storage and versioning of information. The focus at Lichtenheldt is on the document control module. Instead of printing out SOP and attachments, the company stores documents in a central database that all employees can access. The advantage of this storage: Colleagues always work with up-to-date documents. It is impossible to have different versions floating around, causing confusion and error-proneness. Rough: “With the d.3 eQMS system, we are not only increasing transparency and security, but also speeding up the workflows associated with new SOPs.”
The following example shows why the d.3 eQMS from Digital Life Sciences improves SOP management: A new SOP in quality control is on the agenda. An employee writes the document in Word. Instead of running to get signatures of the responsible persons afterwards, he saves the file in the database of d.3 eQMS systems. When editing is complete, a predefined document circulation starts automatically. The first person to see a message in their dls | eQMS inbox, for example, is the laboratory manager, who is asked to check the content of the document for accuracy and confirm the check with a signature. Since a manual signature is no longer possible, two-way authentication comes into play. The laboratory manager uses one password to log into the system and another to place his digital signature on the document.
After this electronic signature, the automated circulation continues. Now the quality control manager finds a message in his mailbox asking him to approve the new SOP. In the final stage, this SOP is released by the head of quality assurance. Step by step, the work instruction thus finds its way through a predefined, purely digital approval process. “Thanks to this digitalization, we have managed to save time and resources while making processes more secure.”
The dls | eQMS also automates training management
Lichtenheldt uses the d.3 eQMS system not only for SOP management, but also for training management. In the past, employees also worked here with Excel lists, with which they documented documents and training courses. Also an elaborate job. Today, the system automatically generates training requirements after the SOP is approved. In doing so, it knows exactly which employees need to be instructed. They receive a message in their dls | eQMS inbox asking them to study the document and take a short online test. A test that can also be created with the software from Digital Life Sciences. “We have over 250 employees that we have to train regularly, once a year for example on personal hygiene. In the past, we had to hold the training courses and exams as classroom events, which required a lot of preparation”, says Rau. “Today, employees can complete the trainings at their favorite time, even in their home office. This means an enormous time saving for us. The system even takes care of documenting the training results for us.”
Complaint management is also digitalized and accelerated
One example: A customer complains that the package leaflet is missing from a folding box. A quality assurance employee receives the complaint and documents the incident in the Deviation Control (DC) module. The system then automatically sends a request to various departments in the company to perform a risk assessment, for example – in other words, to estimate the probability that such a case could occur a second time. If the probability is given, preventive and corrective actions (CAPA) can be triggered via the system, such as the introduction of a belt weigher that can infer an incomplete package from the weight.
“These are all steps that used to be done on paper and now work faster and more securely thanks to digitalization”, explains Rau, who is also convinced by the cooperation with d.velop. “The collaboration was really productive and fun. We experimented with automated workflows together, tested them in day-to-day operations, and kept fine-tuning them until the processes finally worked. Digital Life Sciences has always worked according to the principle of helping people to help themselves. After a short time, we felt fit enough to operate and further develop the system without support.”
Learn more about the Document Control
Get a holistic overview of our versatile software Document Control now.