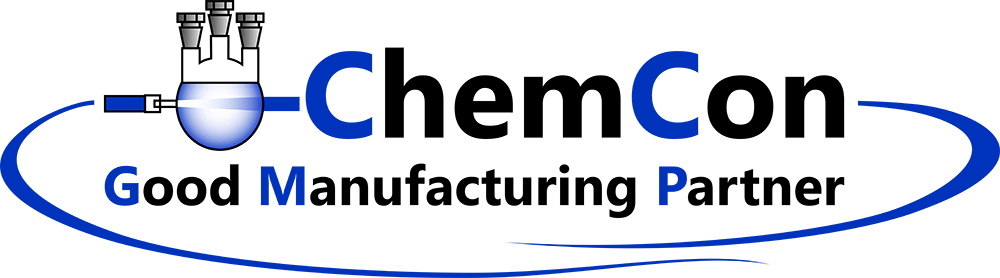
ChemCon saves up to 40 percent of working time in certain sections with digital Document Control
"Updating documents, reprinting, resigning, and invalidating the old documents: The flood of paperwork had completely overwhelmed us after 25 years of company history. We had seen the need to get rid of paper where we could. With the Document Control by Digital Life Sciences GmbH, we certainly save 30 to 40 percent of working time in the documentation. For example, it has become much easier to correct documents. Work has become more efficient overall. Everything is much faster and less cumbersome. Digital Life Sciences is not just a service provider, they work really great with us."
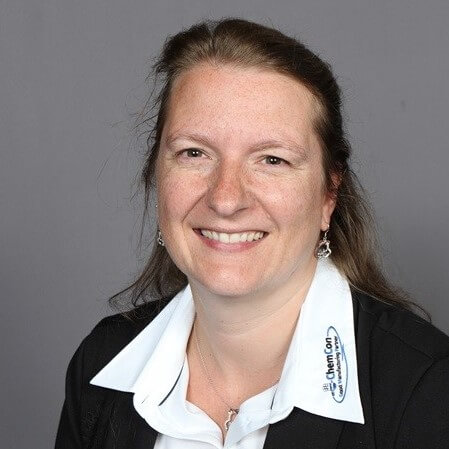
Active pharmaceutical ingredients for combating rare diseases, for emergency medicine; niche products, among others, for ophthalmology and cancer therapy: ChemCon GmbH in Freiburg, Germany specializes in active pharmaceutical ingredients and fine chemicals of the highest quality. For clinical trials or rare diseases, often only small amounts of an active ingredient are needed. This is the niche covered by ChemCon. From smallest quantities up to several hundred kilograms are produced here per year. In this field in particular, the greatest possible precision and documentation are essential.
Standardised working instructions or Standard Operating Procedures (SOP) help to deliver consistent quality. “Updating documents, reprinting, resigning, and invalidating the old documents: The flood of paperwork had completely overwhelmed us after 25 years of company history,” says Ilka Noack, Vice Director of Quality Assurance and Regulatory Affairs at ChemCon GmbH.
Due to the growth of the company during the last 25 years to currently 130 employees, the need for documentation and thus documents has increased significantly. ChemCon struggled with mountains of paper. For example: In the industry, a product synthesis regulation can easily comprise 50 to 200 pages. Updating and revising synthesis regulations and work instructions took a lot of time in the traditional way. Imagine, for example, a regulation of 20 pages in which only a few sentences need to be updated. Despite the fact that the amount of work involved was manageable, it was still a lot of work due to the need for several employees to check new documents and the corresponding number of signatures to be managed.
Updating documents could take days
The often necessary adaptation of documents including printing, distribution, and tracking of the documents plus invalidating the old version as well as archiving could take days for such an update. “The piles of paper on the desks were growing,” says Ilka Noack, “the processing times were long and it felt cumbersome.” For small companies and start-ups, this may still be a justifiable effort in some circumstances, but established companies the size of ChemCon with a considerable product history must reduce this effort. Noack: “We had seen the need to get rid of paper where we could.”
With this in mind, ChemCon GmbH was looking for a digital alternative. Through a market analysis and the corresponding prioritization of the requirements, three providers remained, which the company examined more closely. Among the requirements was that a new digital Document Control could run on the company’s own servers, not in the cloud. “We were looking for a smaller, flexible company and didn’t want a giant provider; this idea also paid off for us in the end,” describes Ilka Noack. She continues: “The client by Digital Life Science GmbH was very appealing in terms of operation and appearance; other software was not as modern and rather old-fashioned, not as intuitive.”
ChemCon GmbH started small at first, with the eQMS solution by Digital Life Sciences and with the Training Management. Workflows for recording and processing deviations (CAPA, Corrective and Preventive Actions) and the Change Control (process) were also among the first processes that ChemCon digitised with the help of Digital Life Sciences GmbH.
Digital Document Control saves paper and makes extensive follow-up work a thing of the past.
Keyword digital Document Control: This is particularly important for Standard Operation Procedures (SOP). How is a chemical analysis to be prepared? How is a product to be manufactured or tested? What test parameters must be observed? What must be taken into account in the event of deviations? What to do when a machine displays an error code?
ChemCon GmbH has standardised work instructions for all processes that are crucial for the quality of the products. This also includes logbooks for the documentation of e.g. process parameters, forms, the documentation of shipping, incoming goods, and much more.
“We now use master documents for many of these processes,” Noack describes, “and that means we always have an up-to-date version. There are no more local copies and no more outdated papers in file folders. All controlled documents, such as SOPs, are also up to date at the relevant workstations only moments after they are updated.”
Any unclear points in SOPs can now be resolved more quickly. Since the process is easier, the employees are often also more motivated to quickly resolve issues. With just a few clicks, the revised versions are on their way to the colleagues who review the documents. “I also always exactly know where a document is currently located in the release process,” states Ilka Noack, “and I can remind some colleagues or ask someone else if the person actually responsible is on vacation, for example.”
Paper is patient, they used to say. Today, the digital Document Control automatically reminds you of passed deadlines. For example, when creating and correcting SOPs or recording deviations. Additionally, corrections and improvements made to SOPs do not have to wait until the next revision, but can be optimised without loss of time shortly after the weak point becomes known.
Digital training management shows Quality Managers the current overview of trainings at all times
Where there used to be piles of paper on desks, today a tidy overview in digital document control shows which documents still need to be updated, checked, or even learned. And Ilka Noack has a bird’s eye view of all documents and trainings that are currently being processed. “This has become so much easier and better with Digital Life Sciences,” says the Quality Manager, “not only in regards to the production and updating documents, but especially when it comes to training management.”
As Quality Manager, Ilka Noack now always has an up-to-date overview of employee qualifications. This way, she knows exactly which employee has already completed a certain training and where content is still pending: “It’s a key benefit that you can see via each colleague’s status what they still need to be trained in and what trainings they have already completed.” If a project is ever paused or revised, Noack can withdraw the relevant documents with just a few mouse clicks.
Summary: By using digital solutions by Digital Life Sciences, ChemCon GmbH benefits from these advantages
- Faster, easier access to documents that are always up to date, e.g. via search mask and mouse click – no more time-consuming searching through stacks of paper
- Current overview of the status of employee trainings and e-learnings: Which trainings have the individual employees already completed? Which trainings are still pending? Mobile access is also possible, for example via tablet or smartphone
- Trouble-free creation and updating of work instructions (SOPs), no more time wasted searching through stacks of paper, no more outdated SOPs due to local copies or superseded binders
- Simple and always up-to-date documentation and processing of deviations (CAPA)
- Withdrawal and revision of documents possible with a few clicks
- Saving of working time which was designated just for the physical handling of paper
- significant paper savings
Up to 40 percent of working time is vacated thanks to digital Document Control.
The switch to digital Document Control saves ChemCon GmbH several 10,000 pages of paper per year, which does not only have a monetary impact, but also significantly improves the company’s sustainability.
Digital documents can be found, processed and forwarded in a split second, and the entire effort of printing, filing, distributing including time-consuming manual tracking is now no longer required. “We wanted to adapt our internal business processes to digital workflows,” describes Ilka Noack, “we made a conscious decision to do so. This has made the company as a whole more efficient. When dealing with documents, we save 30 to 40 percent of working time.”
Each process and workflow is now tagged with attributes, allowing employees to filter targeted information in seconds instead of having to search through tall stacks of paper. Outdated printouts and local copies become no longer necessary as well as accidentally passed deadlines for e.g. the processing of SOPs or deviations.
Ilka Noack: “We have never regretted choosing the digital Document Control by Digital Life Sciences. It was the right decision from the start. In the course of the project realization, a partner-like relationship has been established with our contact persons. Our partners also contact us proactively to discuss new ideas. Everything happens much faster and less cumbersome than we know from other implementation projects. Digital Life Sciences is not just a service provider, they work really great with us.”
Would you like to learn more about our solutions?
Then look at our suitable solutions now.