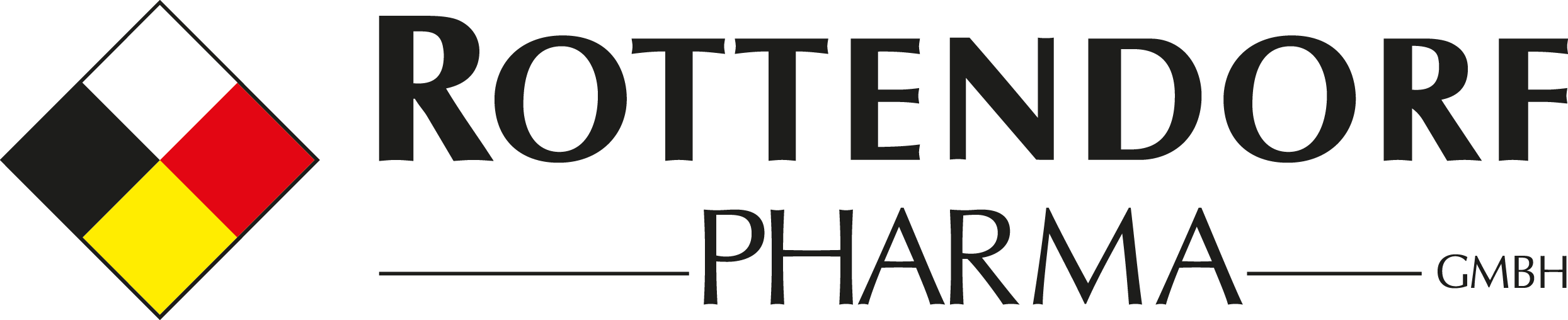
A sweet pill to swallow
"The Digital Life Sciences team has been supporting us for years in making our processes more efficient and digital. In this way, we have been able to successfully implement the DMS, Training Management and VMS in our company in a GMP-compliant manner over the past few years. We are happy to build on our positive experience with the Digital Life Sciences team and currently have numerous projects in the pipeline that will make our documentation more digital, traceable and centralized. Digital Life Sciences GmbH is a strong and long-term partner for us."
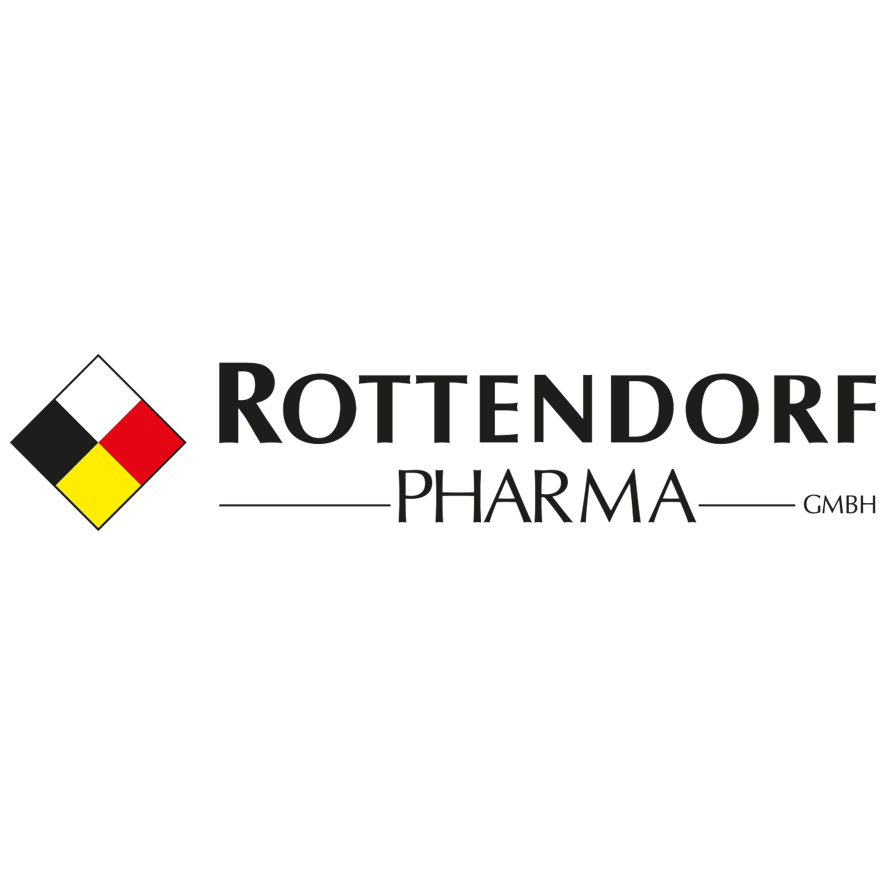
Rottendorf Pharma digitises document control and employee training with QMS dls | eQMS.
Digitisation is not witchcraft. Rather a rather sweet pill, proves Rottendorf Pharma. Since the ever-increasing use of digital systems, the pharmaceutical company from Ennigerloh has already saved a large number of working hours per year in employee training alone – thanks to the quality management system (QMS) dls | eQMS.
Film-coated tablets, coated tablets and capsules: Rottendorf Pharma is a pharmaceutical service company from Ennigerloh near Münster, which has specialized in the development, production and packaging of pharmaceuticals in solid dosage form since 1928. A company on course for growth. The pharmaceutical specialist now employs more than 1,200 people. However, this development also poses organizational challenges for the company. For example, in the management of so-called Standard Operating Procedures (SOP). These are instructions that describe the standardized handling of processes – for critical areas of the pharmaceutical industry.
"This red tape was really our largest pain point"
SOP management cost Rottendorf Pharma time and nerves for years, because it took place entirely on paper. Employees juggled over 900 instructions with up to 40 attachments each. They walked miles around the company to get signatures and pass the documents on to colleagues. They spent hours at the printer and in archives when content changes were due. “This red tape developed into our largest pain point,” recalls Dr. Nicole Freise-Papke, Process Group Leader QA Systems at Rottendorf Pharma. “To save resources and nerves, we therefore set out to find a specialist for digitization solutions in the pharmaceutical industry.” Rottendorf Pharma found what it was looking for at Digital Life Sciences from Gescher near Münster.
Goodbye to miles of walking and wasted paper!
To simplify the management of SOP documents, Rottendorf Pharma and Digital Life Sciences have introduced a quality management system (QMS) called dls | eQMS. This is a platform that, thanks to its modular structure, grows flexibly with companies and simplifies numerous tasks – around the classification, structuring, storage, and versioning of digital information. At the heart of the solution at Rottendorf Pharma: the Document Control module. Employees create new SOPs with this module. This is done much faster than before with the help of templates. The review, approval and release cycle is also accelerated. It is now also performed within the QMS. Signatures are no longer applied on paper, but electronically. Kilometers of walking between departments are now a thing of the past. The same applies to wasted paper, which is a great pain for more and more companies in times of sustainable business. Moreover, the software ensures transparency
"Thanks to d3.life sciences, we gain full transparency in the qualification level of employees"
The onboarding for new SOPs is also accelerated. When a new instruction is circulated, employees receive a message asking them to study the document. If they confirm that they have read and understood everything, a green check mark appears in a qualification matrix. “When it comes to SOP management, we are now completely paperless thanks to the digitization solution,” says Ms. Freise-Papke. “As a result, we gain full transparency on the qualification level of employees much faster than before. And that’s without printed paper or confusing Excel spreadsheets.” In the future, Rottendorf Pharma will therefore also be digitizing other types of documents – again in close cooperation with the experts from Gescher. “We appreciate Digital Life Sciences’ efforts to find an optimal and customized solution for our needs. That’s not something to take for granted.”
Digitization of GMP training saves 120 hours of work per year
Rottendorf Pharma is on course for digitization. And establishes the first company-wide e-learning for so-called Good Manufacturing Practice (GMP) training.
In the past, GMP seminars were held regularly in offices, and the documentation of training and test results was done laboriously by hand. Today, the whole program takes place in the digital sphere. This is made possible by the latest module in Rottendorf Pharma’s digitalization toolkit: E-learning – a module for the digital training of employees. Instead of traditional classroom instruction, employees use the module to create e-learnings on various topics, such as procedures in documentation practice or hygienic hand washing. Documents, audio files and videos to illustrate the learning content can be integrated with just a few clicks. The module can also be used to design a final exam in an equally time-saving manner – including elements such as text answers, cloze texts or puzzles.
QA employees then provide the prepared e-learnings and the final exams to their colleagues from the respective departments via the task inbox. Having passed the exams, the software automatically updates the team member’s qualification level in the qualification matrix. This allows to see at a glance if only employees who have been demonstrably successfully trained are performing the relevant activities. “By implementing e-learning for company-wide GMP training, we save about 120 man-hours per year,” explains Dr. Freise-Papke. “After this successful pilot project, we therefore want to digitize even more company-wide training in the future.”
Learn more about the E-Learning software solution
Get a holistic overview of our versatile E-Learning solution now.